
“What do you want to be when you grow up?” It’s a question we’re all faced with at some point as a child, and most of us will have a pretty creative answer. Sadly the majority never go on to realize these childhood dreams, but there are a select few like Christian von Koenigsegg who never give up on their goals. I think it goes without saying then that visiting the workshop of a man who dreamed to one day make the most extreme car in the world was an experience that defies words; but I’ll attempt to do it justice.
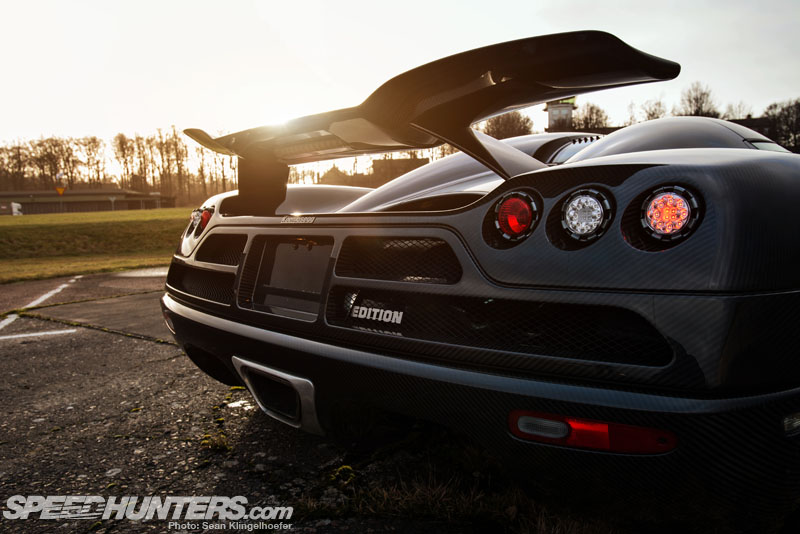
There are ton of numbers and phrases I could throw about to describe Koenigsegg and their cars, but bearing in mind that the Speedhunters audience consists mostly of petrolheads, I’ll skip the basics – there are plenty of other places online where you can get that info. Besides, the numbers alone don’t even begin to describe the essence of the brand.
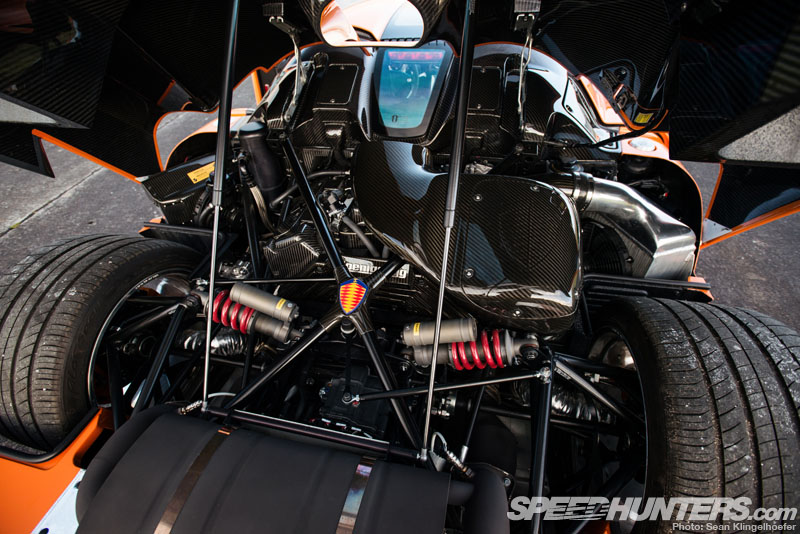
If you have been living under a rock or just have a short attention span when it comes to hypercars and have some catching up to do, Drive has an excellent series of videos worth checking out – but be prepared to spend the next hour glued to your computer screen. In short, Koenigsegg makes some of the most badass cars on the planet.
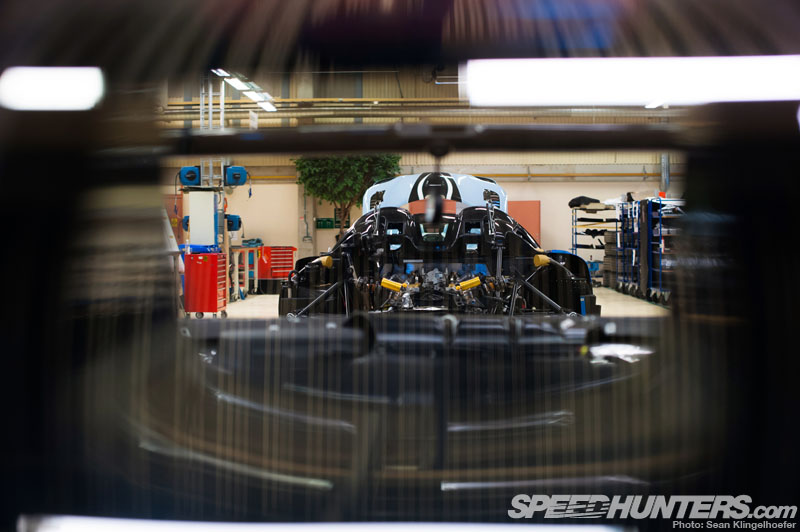
Of course building one of the most high performance cars of all time costs a pretty penny, therefore they aren’t very common. In fact, before we headed to the factory I had never even seen a Koenigsegg in person. Living in Hollywood I see Ferraris, Lamborghinis and Aston Martins on a daily basis, hell, even Bugatti Veyrons aren’t a rare sight, but I’ve never once seen a Koenigsegg stateside.
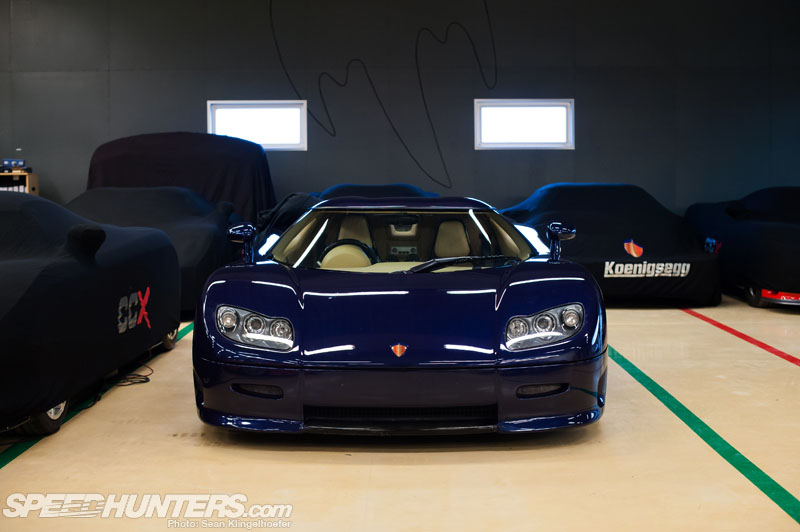
Fortunately Koenigsegg were kind enough to host Rod Chong and myself on very short notice, and because of that I’ve now seen two dozen, spanning the entire model history of the brand starting with the original CC8S.

Not only that, but I got some time to sit down with the man behind the cars, Christian von Koenigsegg, to see what makes him tick and try to figure out why he’s building such crazy cars. It was a lot to take in, and even now I’m still absorbing much of it. A once-in-a-lifetime experience no doubt.
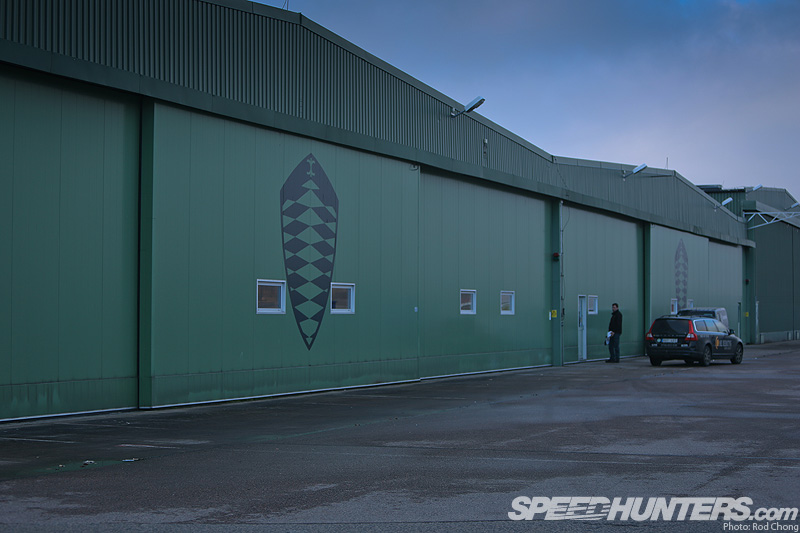
As most of you already know, the Koenigsegg factory is a former fighter jet hangar. Not only is this cool because, well frankly, jets are badass, but it also has some additional perks; like being a few hundred feet away from a massive runway on which you can test these vehicles. But there are other residual benefits too, some of which we’ll get into later.
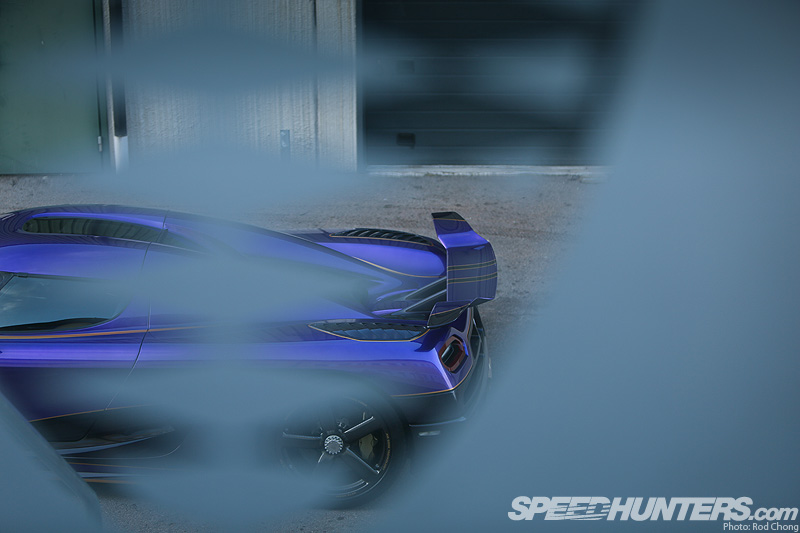
The day that Rod and I made our way down to Ängelholm happened to be one of utmost rarity – the day that a completed car would be delivered to a customer. When you consider that to this day Koenigsegg has only built 100 vehicles in just over a decade, you can see just how infrequent such an event is.
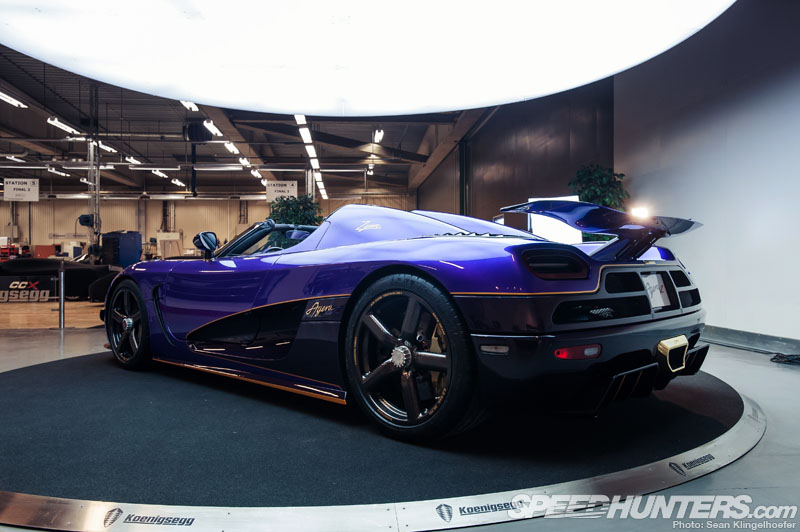
To celebrate the monumental occasion, Koenigsegg places a completed car on a special platform with a massive overhead light bank – a killer place for buyers to see their hypercar for the very first time. However cool as it was to see such a magnificent machine all buttoned up and shiny, what I was really looking forward to was seeing one in pieces.
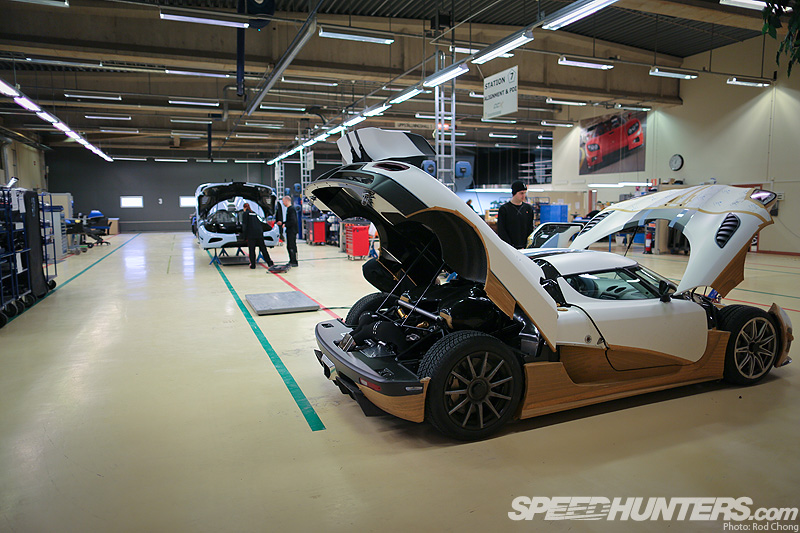
Fortunately there was a car in virtually every single stage of production when we visited; from a bare monocoque all the way up to the completed example we just saw, and every stage in between.
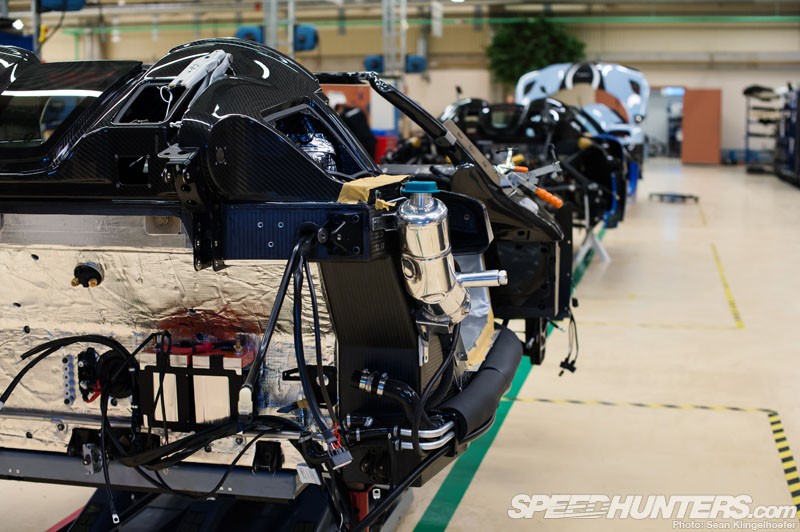
Built in numerous stages in a layout similar to an assembly line, the Koenigsegg philosophy adopts time saving strategies but requires a little more of a hands-on approach compared to an ordinary car. The process starts when the factory receives the fresh carbon tub which then goes through a total of seven stages before being delivered to the customer.
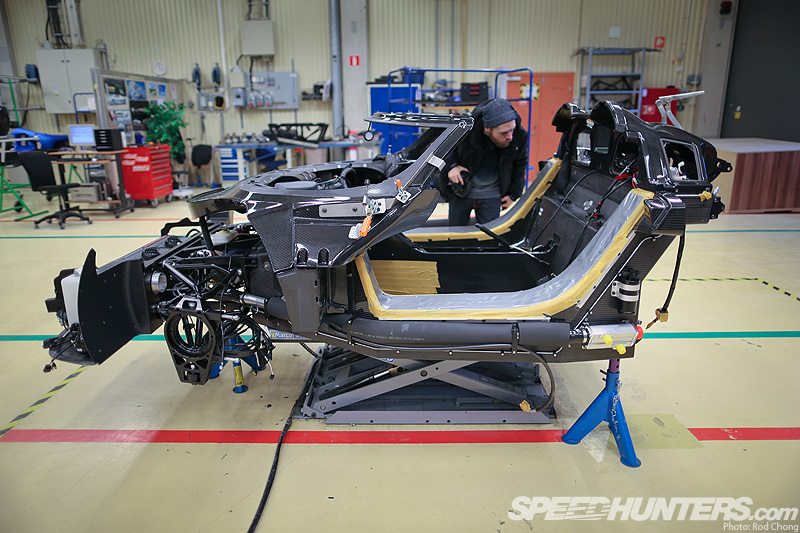
Seeing the car in this early form makes it clear how serious of a car the Agera is. As I examined the monocoque I was actually pretty surprised by how familiar everything was. I’ve actually come across this architecture dozens of times, in prototype sports cars! The model by which Koenigsegg builds its cars from is taken right out of the pages of race car construction.
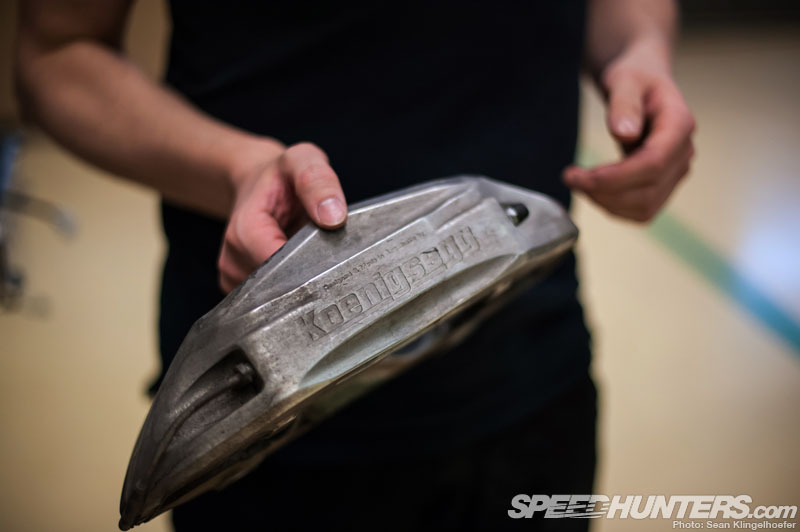
While the vision has remained the same since day one, with each passing year Koenigsegg does everything they can to bring more and more of the processes in-house, with the eventual goal of total self sufficiency on the near horizon. In all honesty I’d say that the desire to bring everything under the same roof borders on maniacal.
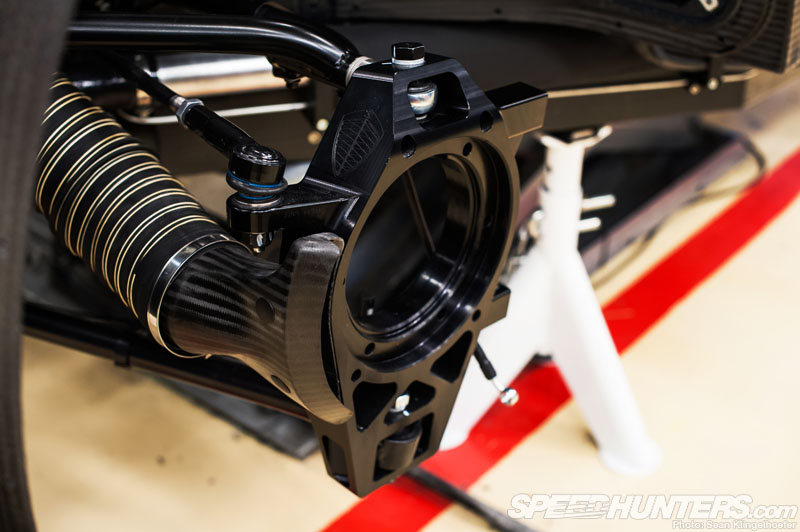
Even today the vast majority of the components are fabricated and assembled on-site in Sweden. In the rare occasion that they cannot manufacture something themselves, Koenigsegg prefer to work with local companies, giving the cars their unique Scandinavian flair. Get a load of the size of the bearing carrier in the upright for example – I’ve never seen a wheel bearing half that size before!
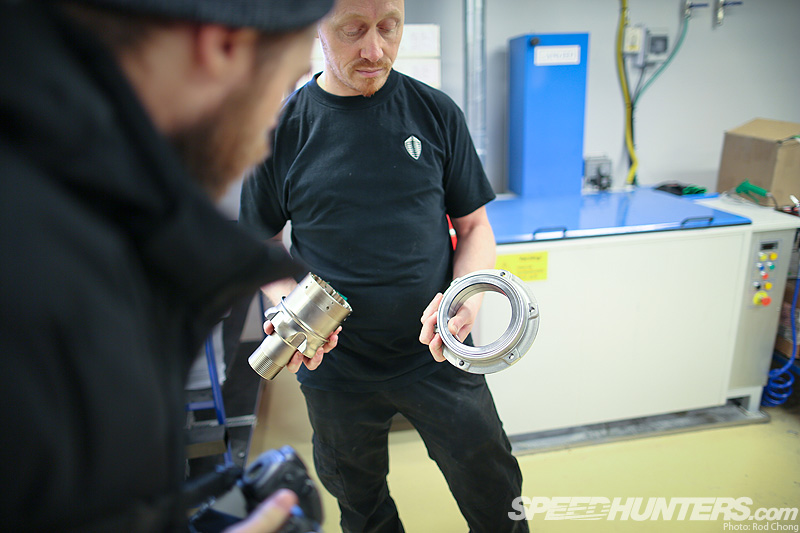
But that’s because Koenigsegg doesn’t use a conventional wheel bearing in their cars… they use a bearing originally designed to support the main rotor shaft of a helicopter! When the factory was taken over and decommissioned from aviation, many of the employees and parts bins were carried over into the operation, hence how innovations like this came about.
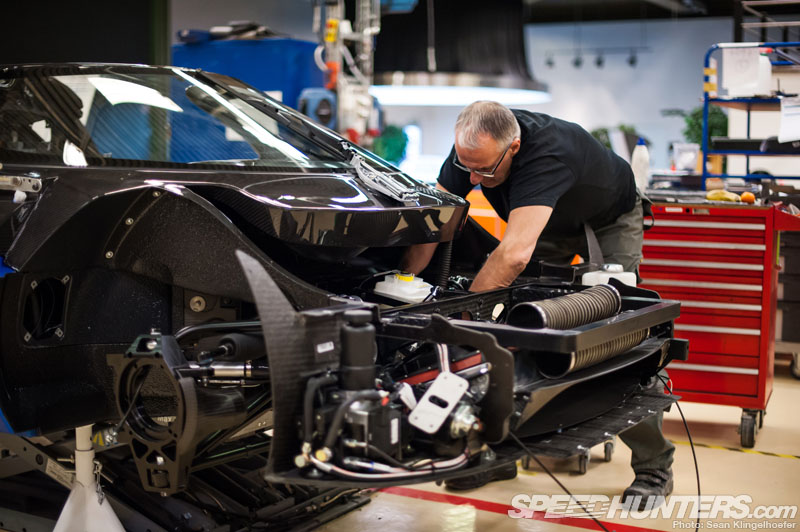
Anyway, the next step is to attach the front bulkhead to the tub along with miscellaneous peripherals. Just about everything on the car is designed in a modular fashion, which is efficient, rigid, lightweight and safe. This is a theme that is carried through practically every nut and bolt on the entire car.
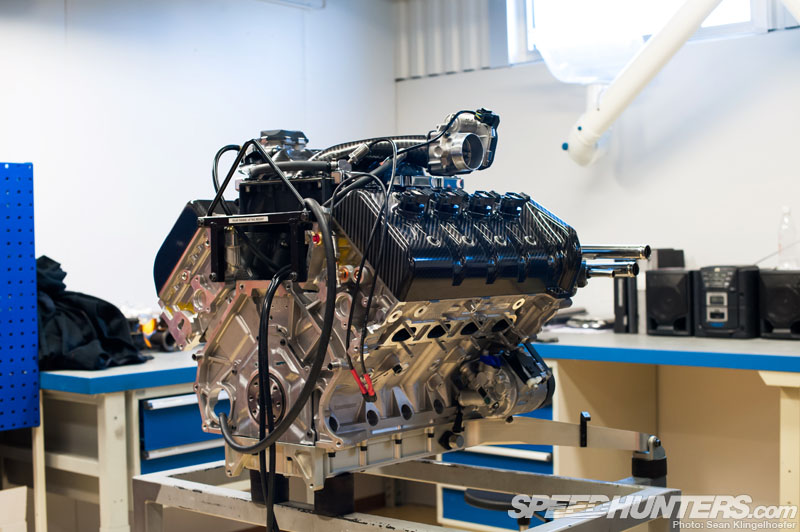
Meanwhile, in the engine room the motor is being built and tuned for the car. This is one area that really sets apart Koenigsegg from the other hypercars out there as this is a completely bespoke power plant, not something bought from the Germans and stuffed into a crazy looking body. On paper it is an all-aluminum/carbon 5.0L V8 that produces 1,140hp, but up close, it’s a work of art.
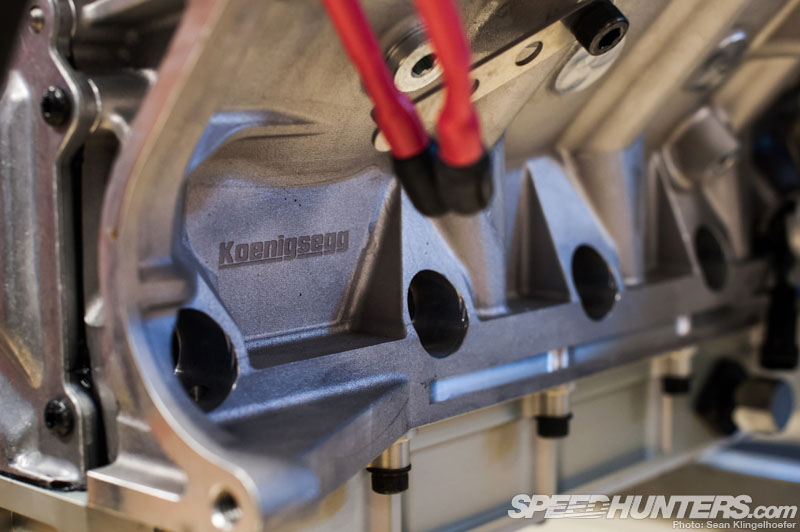
Efficiency and optimization is the name of the game and in addition to being a beastly power plant, it’s also part of what makes the Agera handle so well. The engine is actually a stressed member of the suspension, which makes it an integral part of the chassis mounted directly to the tub with the gear box hanging off the other end – again, just like a race car.
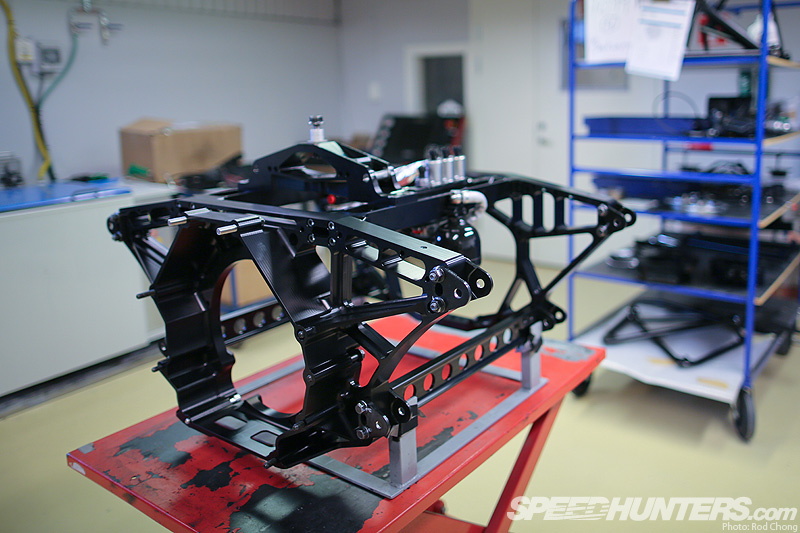
Here’s a look at the cradle that bolts to the rear of the engine block and houses the gearbox. This is also where the part of the sophisticated triplex suspension comes into play. More on that later…
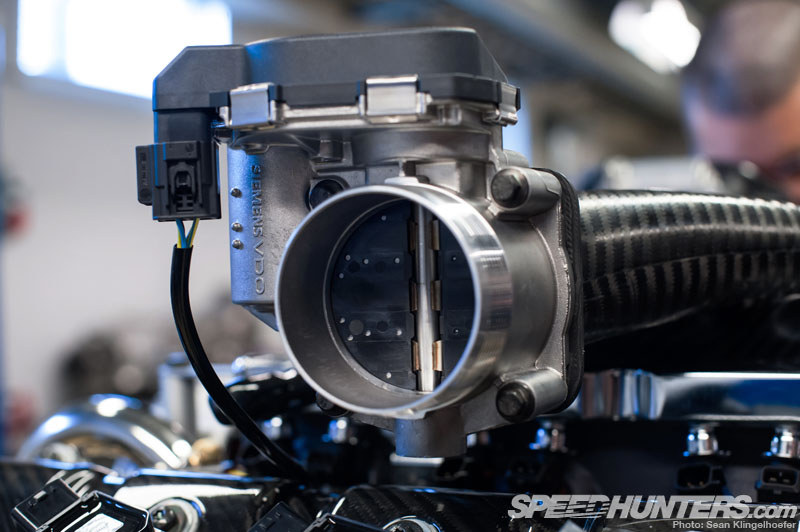
There are a number of innovations that can be spotted all over the engine. I was intrigued to hear about the ingenious flex-fuel system that can automatically detect the alcohol content of fuel and recalibrate the engine parameters on the fly. But even had I never heard that, I could stare at the power plant for hours simply drooling over its looks.
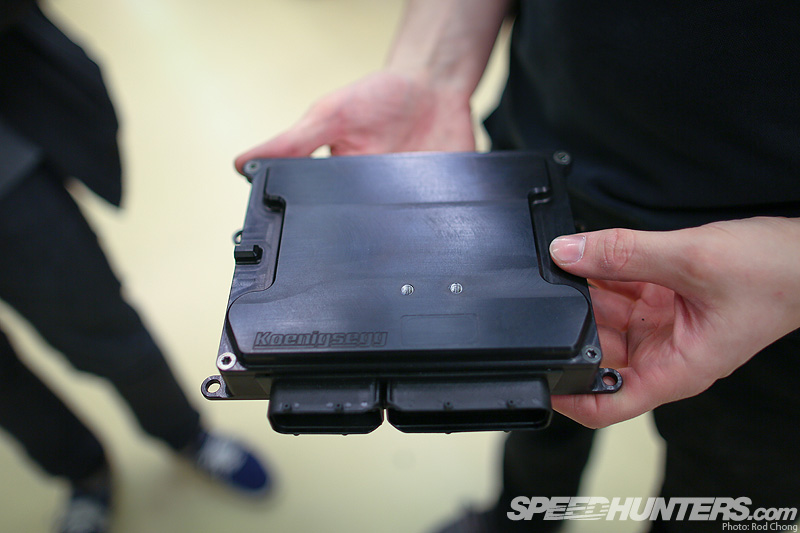
What’s equally impressive is that Koenigsegg has taken on the task of developing their own ECUs. While it might seem cost-prohibitive, as one of the workers explained to me, when you’re making cars at this high of a level in low volume, it’s actually much easier and more economical to make your own boxes. If and when a problem arises, it can be solved and implemented right there on site, and the same goes for prototyping or R&D.
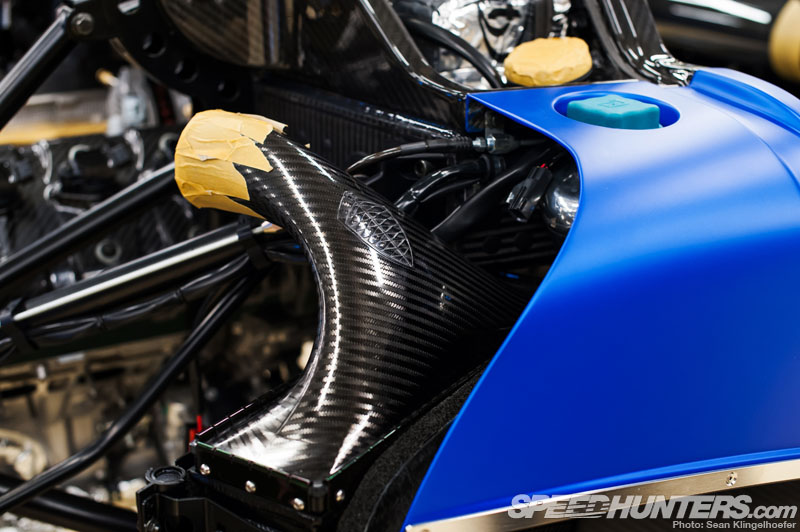
But perhaps the area where the company has put forth the most effort to develop and innovate is in the realm of carbon fiber. It seems like virtually every component on the car is made out of carbon. In fact, to the best of Koenigsegg’s knowledge, the Agera is constructed out of the highest percentage of carbon fiber of any car ever built.
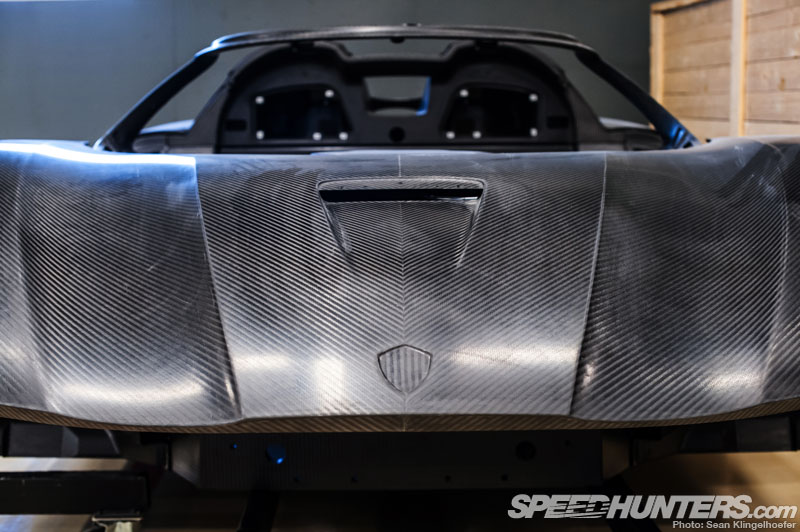
I don’t think I need to explain to you guys why carbon fiber is a desirable material to fashion car components from, let alone why it is so widely used in high performance applications. What is worth mentioning is to what length this love affair with carbon fiber has gone to. Nearly every piece aside from the tub (which they’re working on securing tooling for now) is made on-site in Ängelholm!
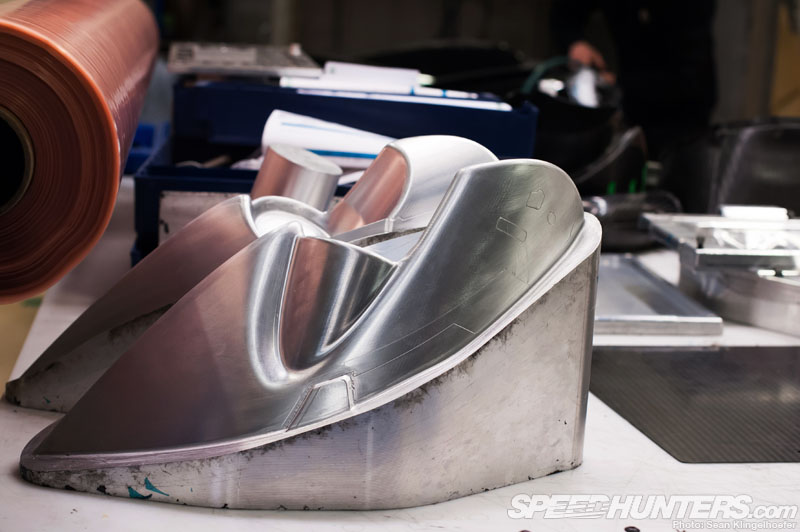
The Agera is comprised of over four hundred individual pieces of carbon, and practically every last sliver is laid and cured in-house. As a matter of fact, Christian von Koenigsegg has actually been experimenting with carbon fiber longer than he’s been making cars.
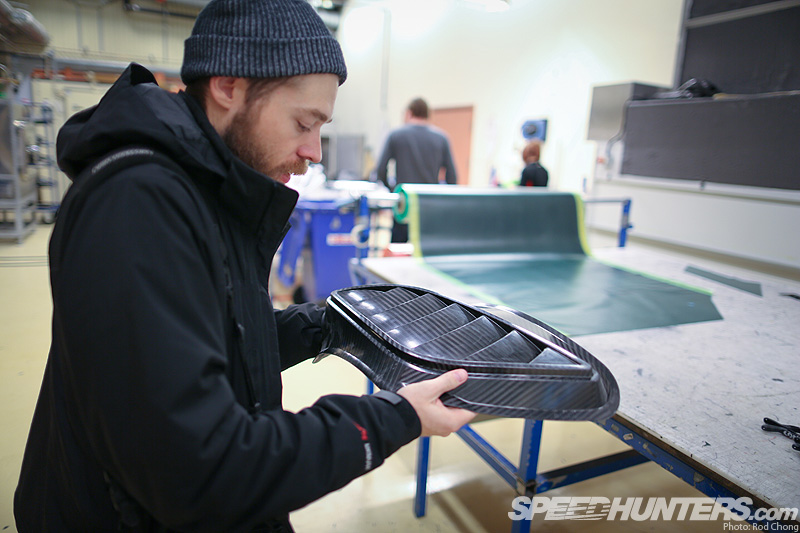
Every component is made from top-grade dry carbon, where the resin is pre-impregnated into the carbon sheets, hence the nickname “pre-preg carbon”. In addition to sounding really cool, this type of carbon allows for more extreme shape forming and uses less resin resulting a lighter part. If you’ve never held a dry carbon part you’ve got to do it – it’s mind blowing how something can occupy so much space yet weigh so little.
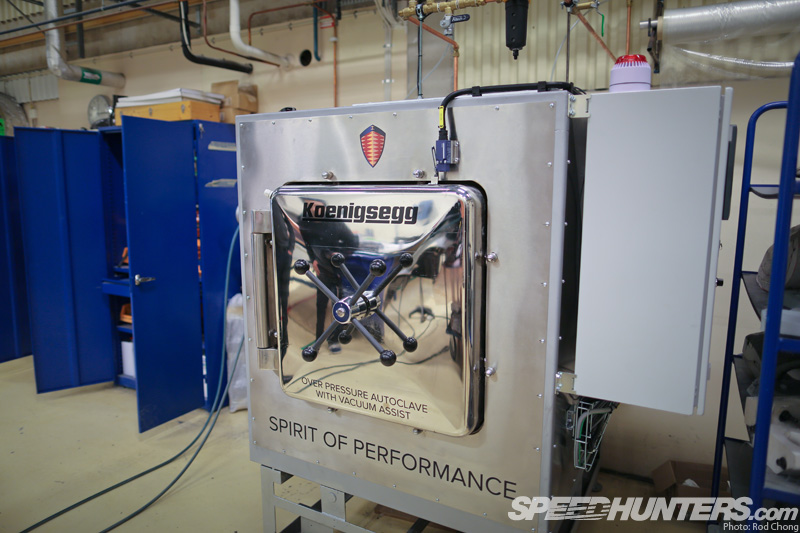
Koenigsegg currently have several autoclaves under their roof, with this being the smallest one used for miscellaneous bits and pieces.
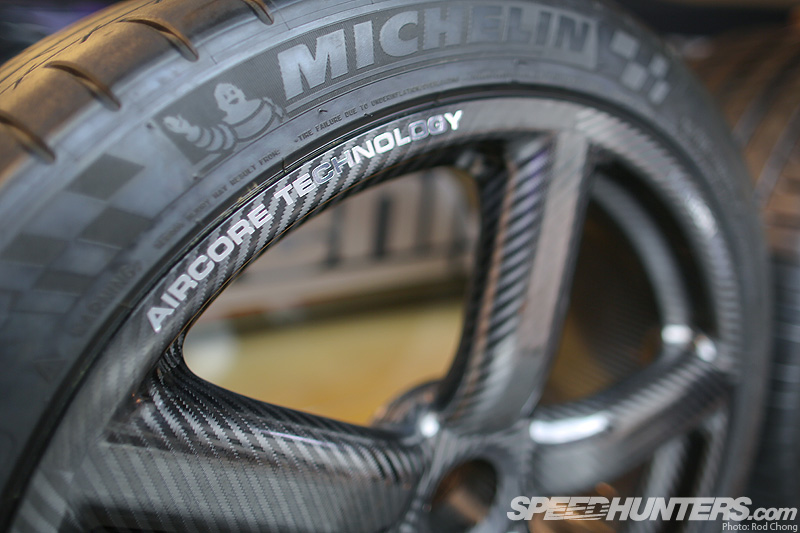
Over the years carbon has become such an integral component in the manufacturing process of Koenigsegg cars that it’s practically synonymous with the brand. One of their most recent innovations is their newest Aircore wheel, which is hollow and made almost entirely out of carbon…
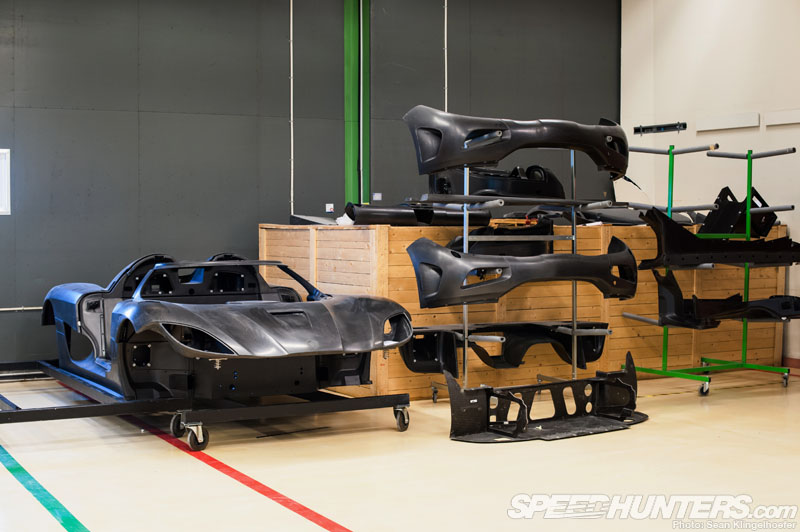
…as is basically the entire car! Here you can see the majority of the bodywork of an Agera in its naked state. I don’t think there’s a panel there that weighs over 10kg (22lbs)!
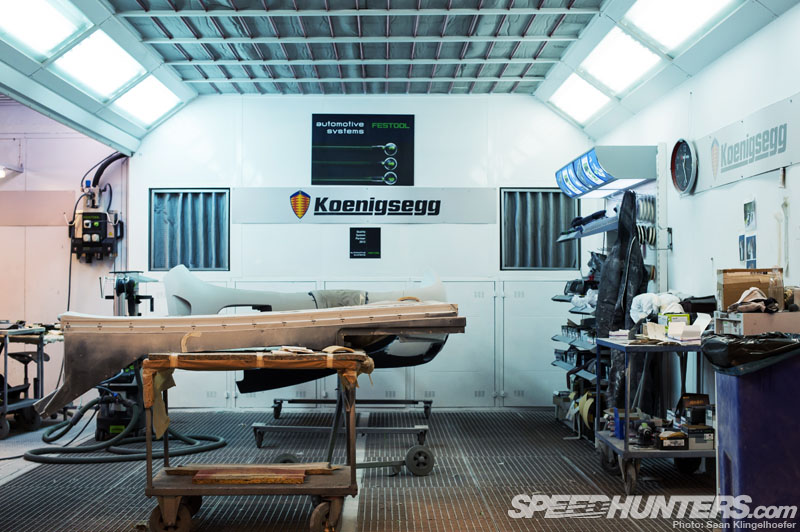
Once the parts have been formed, they head into the paint booth to be sprayed. With the paint cured and color sanded, the parts are then sent over to a special polishing area to be buffed to perfection before being installed on the car.
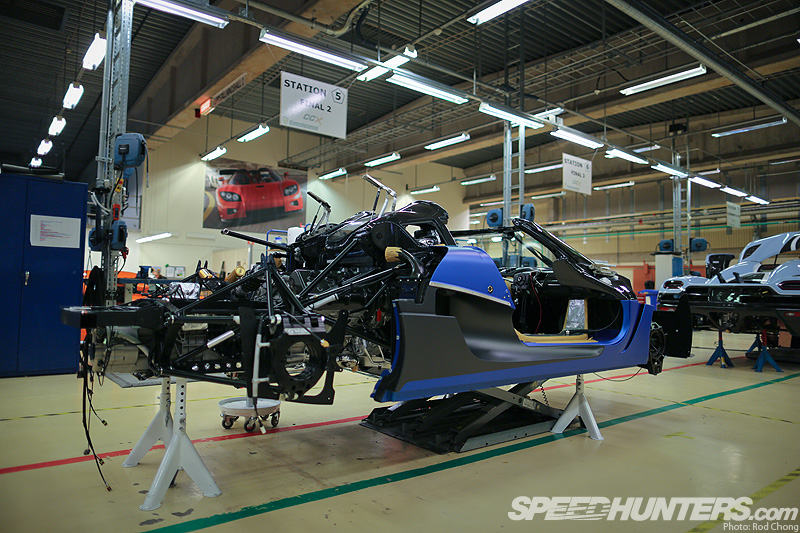
Back at station five, some of the newly painted pieces and powertrain start coming into the picture. At this point the car is starting to take shape and you can already tell you’re looking at a Koenigsegg. This is also where the tricky new rear suspension starts to come into play.
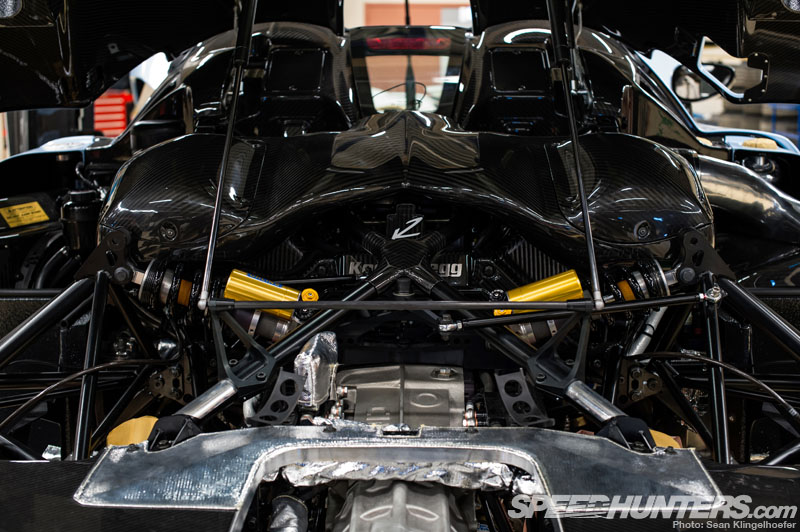
Although the third damper hasn’t yet been installed in this image, we’ll just have to pretend it’s there and connecting the left and right sides from the vacant holes just above where the shock absorbers mount. Koenigsegg calls this their “triplex” suspension, but this technique has been used in motorsport for years and is more commonly known as a third-element setup. Keen readers will recall seeing this on the Lovefab NSX from Pikes Peak. While originally invented to ward off aero-load, the effect on the Agera is improved anti-squat and a smoother straight-line ride.
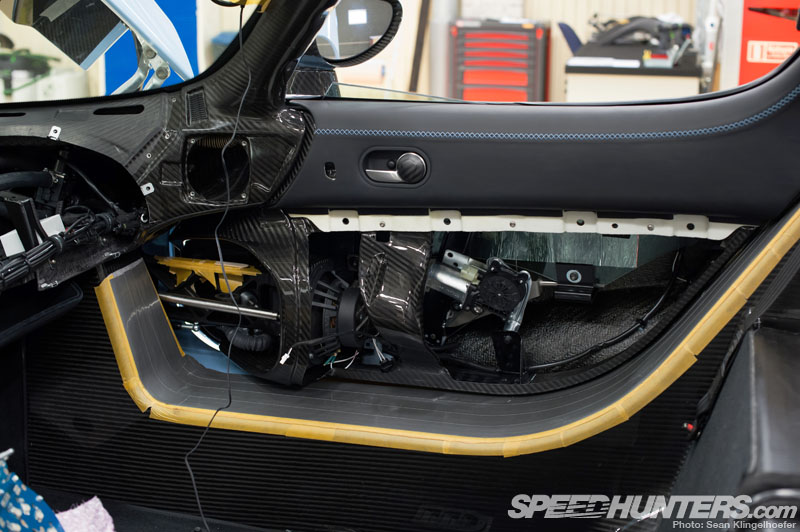
Once the car moves to the sixth station it’s getting very close to completion. Here we can see the internals of the door panel being fitted before eventually being covered by a built-to-order custom panel. Note the door-mounted compact subwoofer. Even a hypercar needs a little bass!
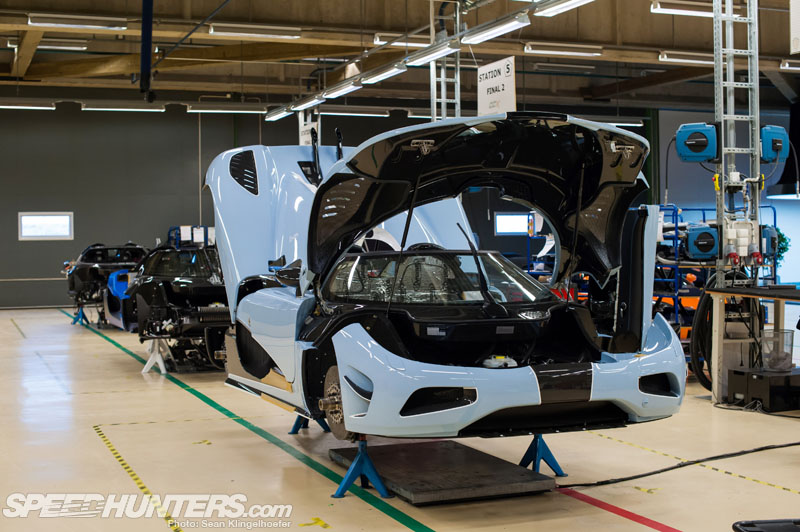
Once the rest of the bodywork is fitted the car is really starting to look finished. By the time it leaves this station it can do so under its own power and from here it moves on for final inspection. Since every car is handmade and crafted to perfection, it shouldn’t come as any surprise that every single component on the car is tested, checked and verified before the car leaves the facility.
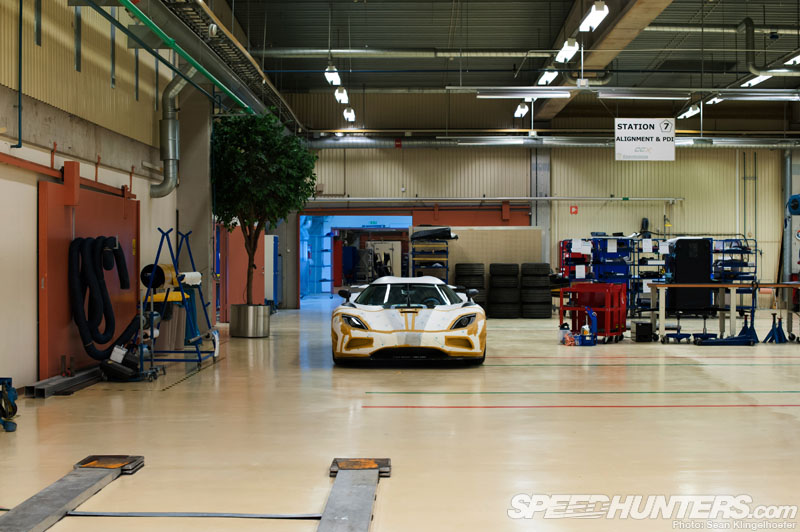
This includes doing high-speed runs, dyno tuning and other fine-tooth comb scrutiny. Although you have to pay a whole lot for an Agera, Koenigsegg go above and beyond to make sure you get exactly what you pay for and then some. Seeing that level of obsession was impressive. Saying that these guys know a thing or two about attention to detail would be an insult – they’re rewriting the book on perfection and you need to look no further than any one of their completed cars to see it.
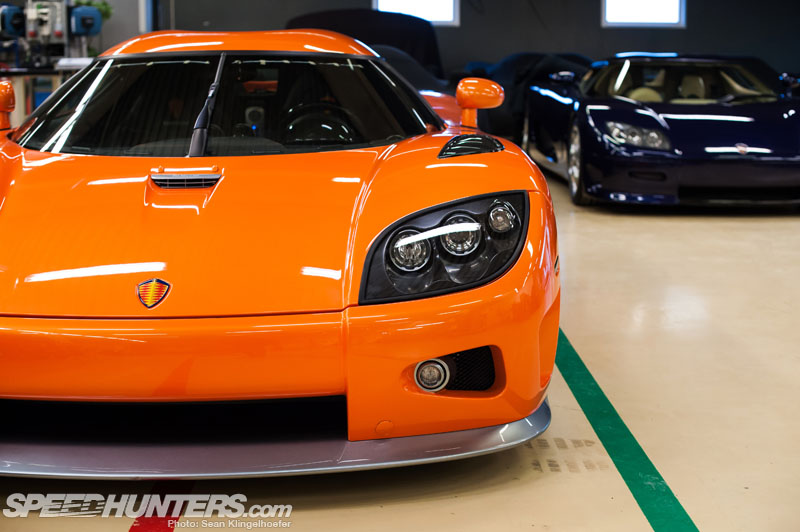
When the assembly tour commenced I had to pinch myself to make sure I wasn’t dreaming. Much like the iconic Porsche 911, Christian von Koenigsegg’s original silhouette hasn’t changed much in ten years. The basic concept right from the start was to simply make the best, most extreme car possible. With each and every passing day that commitment is upheld, one small revision at a time. It’s obsessive for sure, but something Christian clearly enjoys very much.
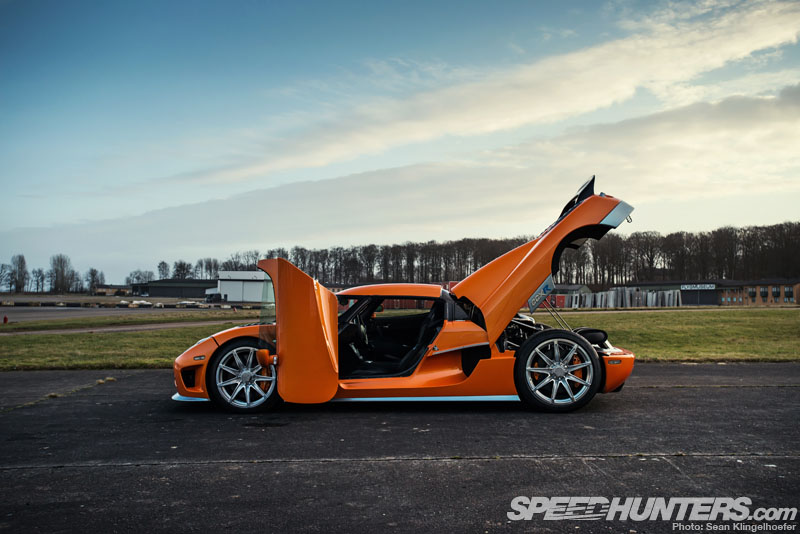
Not wanting to leave empty-handed I asked as politely as I knew how if it might be possible to go outside and shoot one of the cars. The difficult thing about shooting a Koenigsegg is finding one to photograph in the first place. As funny as that might sound, there aren’t exactly a ton of them on hand; once a car is sold the owner picks it up, typically never to be seen again…
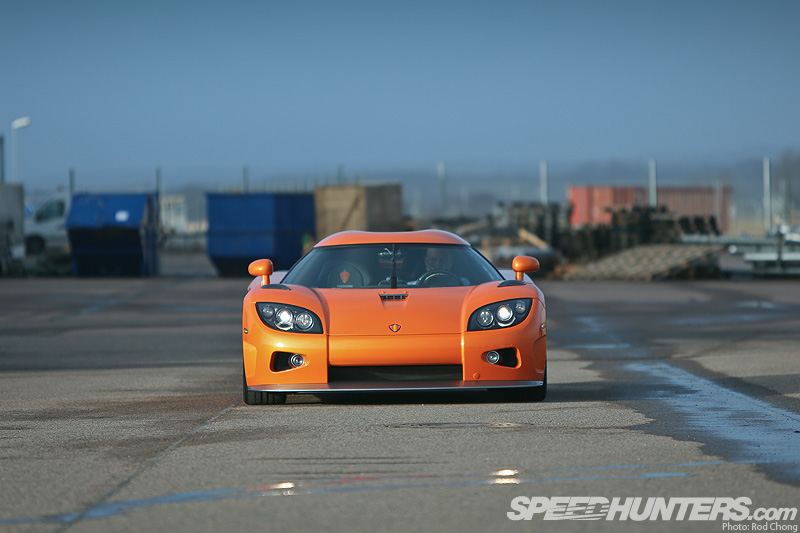
Nevertheless, there were a few cars in the Koenigsegg collection, as well as several customer cars in the shop that were back for repair and the boys were happy to make my dream of shooting a Koenigsegg a reality. It was somewhere around this point that it struck me just how much Christian loves these cars. He even drove them out personally.
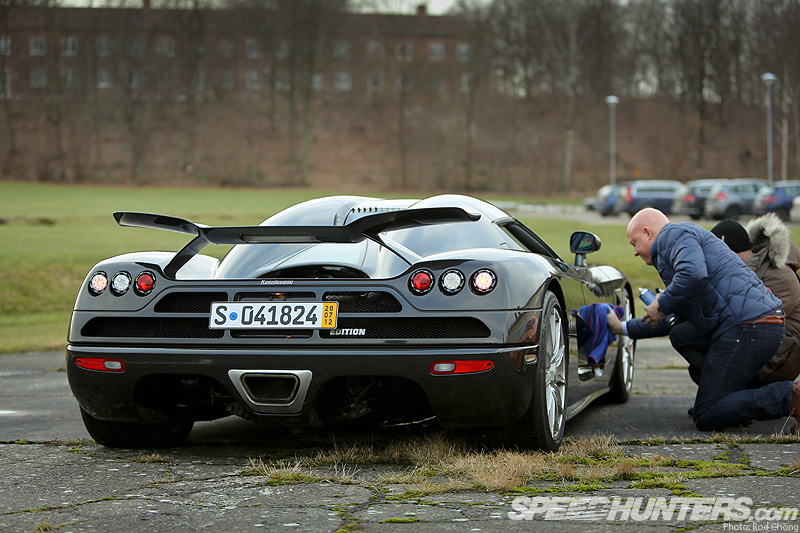
Not only that, but he even got down on one knee and started cleaning up the cars for the shoot! How many people do you know that can say they had the owner of a multi-million-dollar hypercar company as their car prepper? Pinch me again, surely I’m asleep.
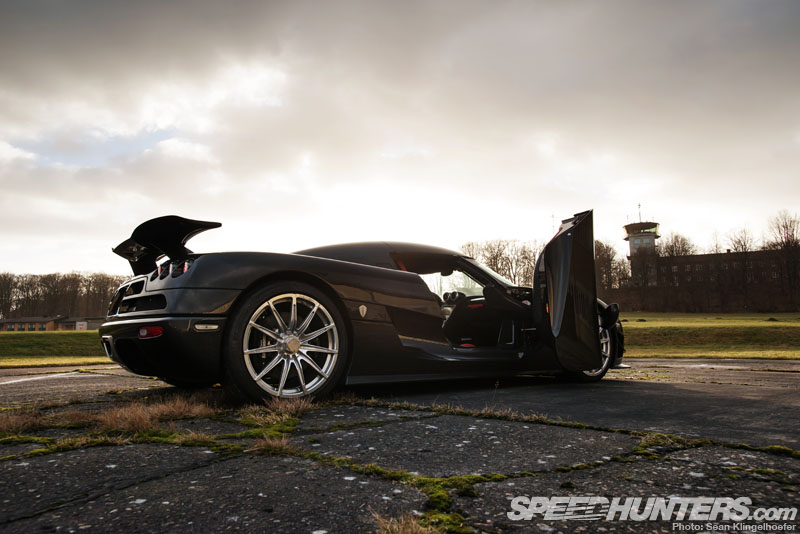
For most of the day the weather didn’t seem to want to participate, instead defaulting to the typical look of a Scandinavian winter: grey. Then by some miraculous stroke of luck, as soon as the cars were positioned and my camera came out, the clouds parted and the sun broke through.
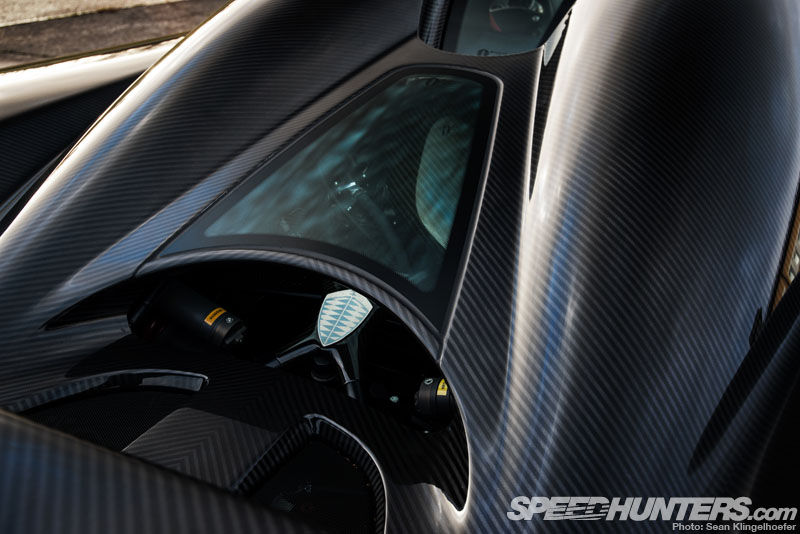
I could think of no better light under which one could enjoy the marvelous curves and details in the carbon fiber body. I discovered the shape of the CCXR to be a little deceiving from most pictures I’ve seen; in person I found the car had lots of detail and style lines that aren’t usually reproduced well in photos.
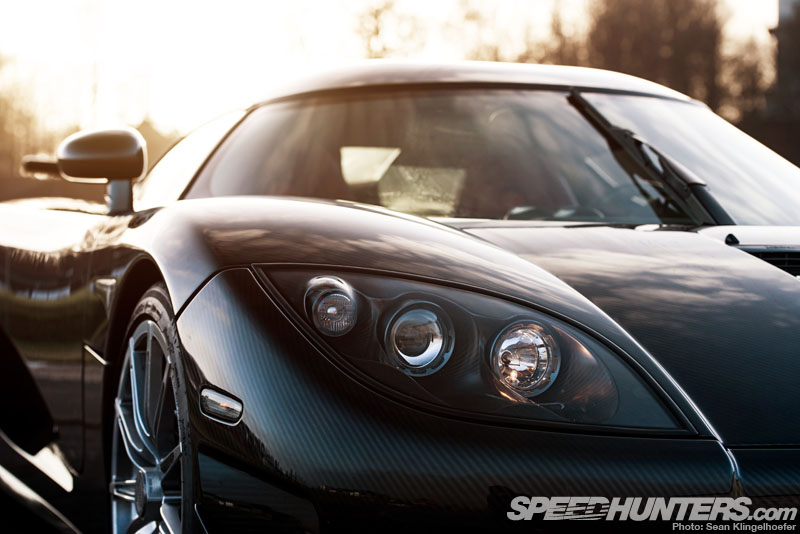
Although the design has been made obsolete with the introduction of the Agera, it certainly doesn’t look dated. Then again, you could make just about anything out of carbon fiber of this quality and it would appear to have come from the future.
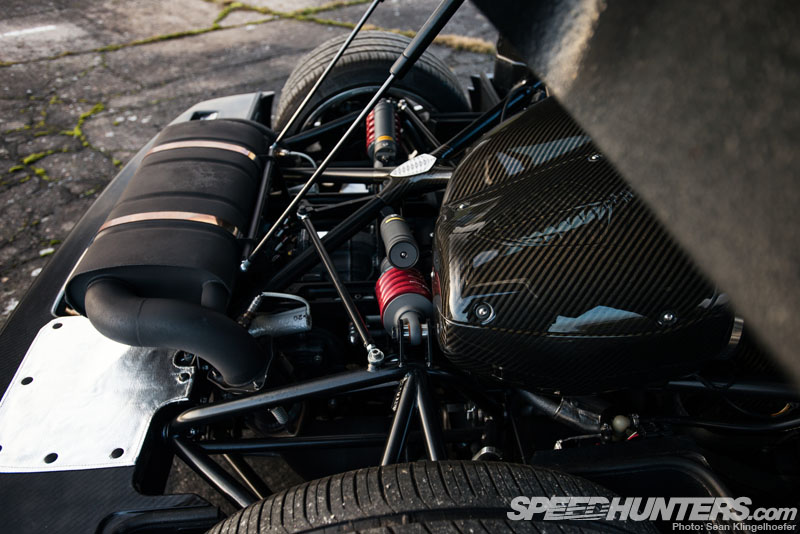
It’s interesting looking at the different parts of the CCXR and seeing how the car has further evolved into the Agera. Again the improvements aren’t necessarily measured in leaps and bounds, but taking one chip after another off the block has kept Koenigsegg at the front of a very competitive market.
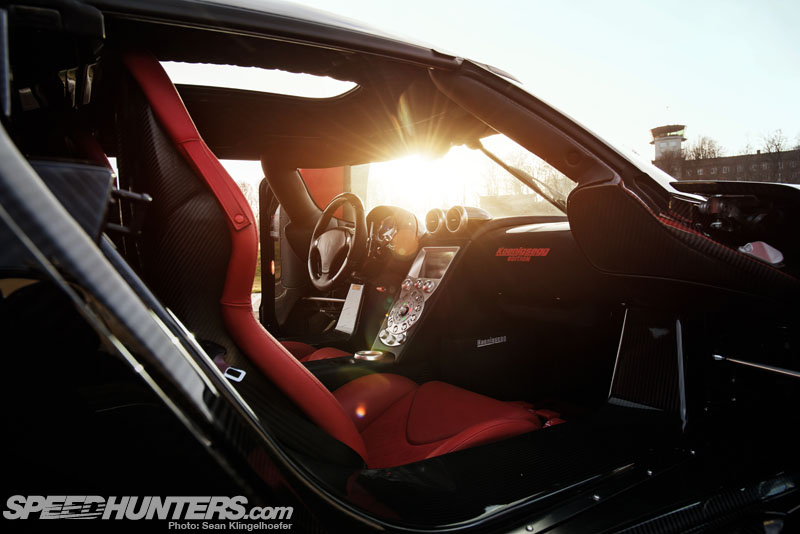
With a hypercar you can’t skimp anywhere, and even if you could, Christian would never allow it. The cockpit resonates this truth and is a sight to behold. It’s achieved the perfect combination of bling, sophistication and raw performance.
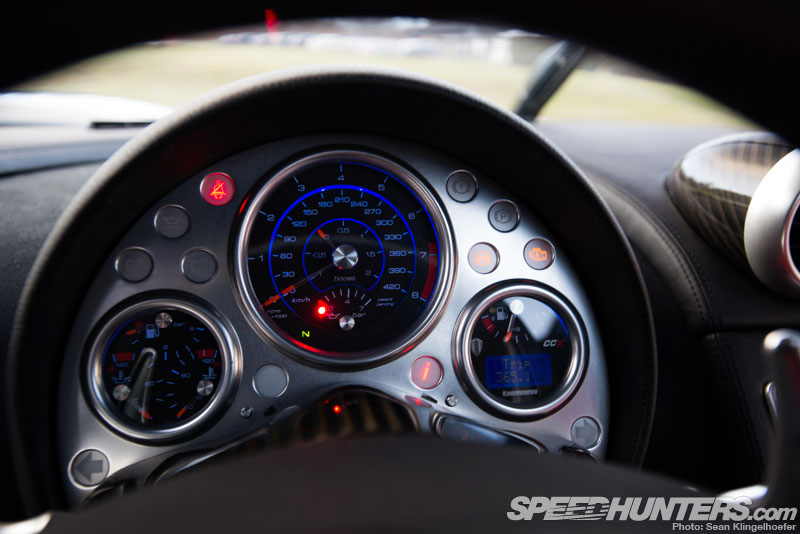
The dials may be the one area where the CCXR does begin to show its age, as the newer cars are fitted with completely digital interfaces. Nevertheless, this classy traditional gauge cluster is still a sight for sore eyes and loads better than what most of today’s cars come equipped with.

The fine craftsmanship of each and every component more than make up for it. After seeing how every last detail is a finely chiseled work of art and a tactile treasure to the touch, it no longer seems civilized to make a turn signal stalk out of plastic.
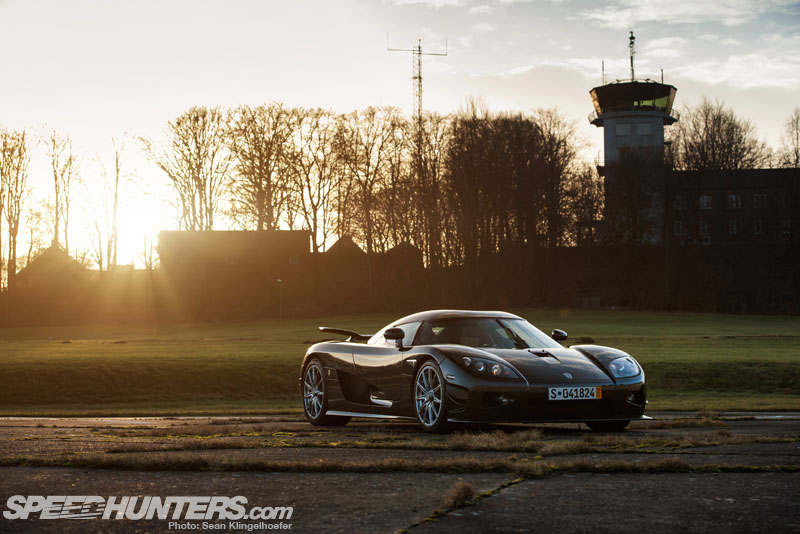
Just being around a car like this makes life better and I can only imagine what it’s like to actually drive (let alone own) one. The sheer brilliance and beauty of this complex object is buried in every last detail. You can rest assured that no matter what bit of the car you see, whether the smallest detail or the car as a whole, you can instantly tell that you’re dealing with something superlative.
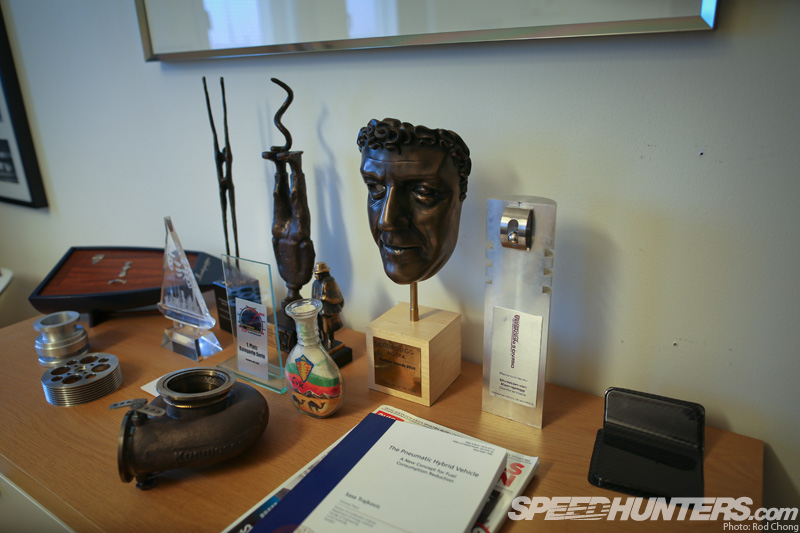
Over the years this unique approach to building the most well rounded hypercar has earned the brand a lot of recognition and countless awards. Some of them are solely based on design, like the prestigious Red Dot design excellence award and the National Swedish Design Prize – a serious feat considering the entire country basically revolves around good design.
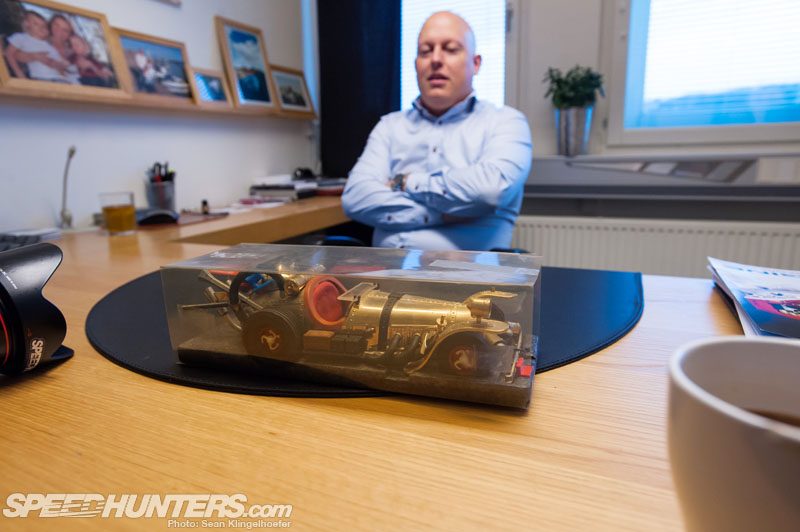
Before hopping on our flight back to Stockholm we spent our last few minutes at Koenigsegg talking to Christian. I didn’t have a formal interview planned, I just wanted to pick his brain a bit and see what his philosophy was and why he’s building such mental cars. Although our time was brief, I completely understand why there isn’t another car on the planet quite like the Koenigsegg – simply because there isn’t another person like Christian.
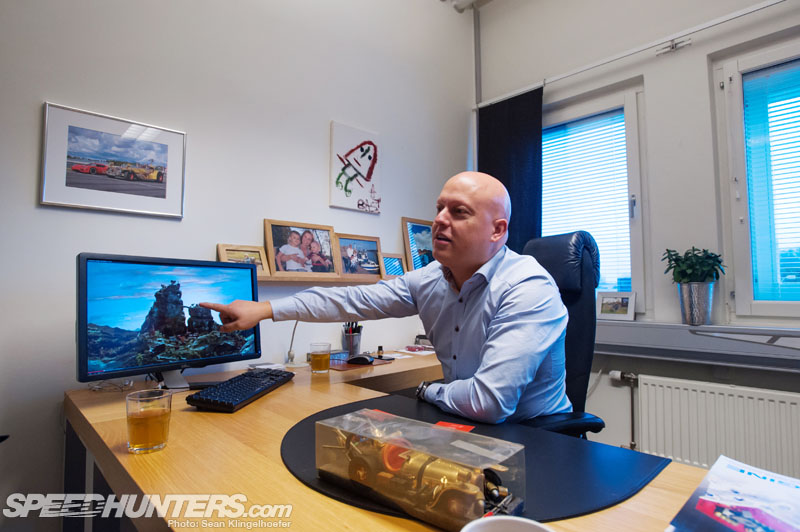
After making us some coffee and tea (and I do mean Christian literally made it himself, he didn’t have an employee do it), he came in and started telling us about an amazing stop motion film called “Flakypa Grand Prix” that inspired him as a child to one day build his very own car. In the movie, a man who lives on top of a mountain builds his own race car to compete in the Grand Prix, ironically funded by none other than an oil sheik.
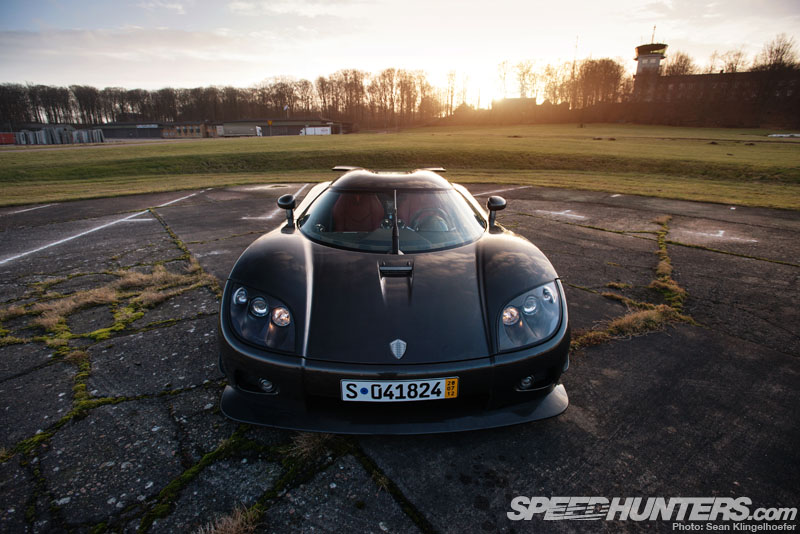
Christian said that as a boy, he didn’t yet realize that this was purely make-believe, so he thought why not have a go at it some day. As with each and every one of us, that little boy is still very much alive and well inside of von Koenigsegg and to this very day he’s still pursuing his dream of building the ultimate car. The parallels that exist between the movie and Christian’s own life are too many to count. If there’s anything to be learned from his story it’s that life’s too short to not follow our dreams – no matter how ambitious or foolish they may be.
More stories about car builders on Speedhunters
More stories by Sean Klingelhoefer on Speedhunters
– Sean Klingelhoefer
sean(at)speedhunters(dot)com
Instagram: seanklingelhoefer
Additional photos by Rod Chong
Ford modular v8
2 things, apart from the fact that koenigsegg really did a great job with the development of their car.
The engine is NOT made in house,Koenigsegg doesn't have nor development or a production line
to build their own complete engine. In fact it is a heavily reworked Ford modular engine.
They don't even make the tub in house, so the expertise with carbon manufacturing isn't all that remarkable.
Finally you can't compare a koenigsegg to the sheere unbelivable detail and depth of engineering, that
for instance pagani has. Regarding the engine I think that a absolutely bespoke AMG V12 developed power
is not something you just get by filling out a custom order form with mercedes.
McLaren F1 buys there engine from them too.
hubbard_fool If you look at the way carbon fiber is made, Youll realize that its more than just the Area of carbon fiber. Your looking at Volume of carbon fiber meaning that the stiffeners used for this are used much more sparingly. Look up how carbon fiber is made and youll understand how he can say that
@HelloHello First, he said they are working on the tooling for the tub now. Second, the detail comment is strictly your opinion. Horacio Pagani and Christian von Koenigsegg chased and accomplished the same dream. They both build beautiful, high performance cars. Third, your second to last statement seems to have been written in a total lapse of intelligence. Last, you're an idiot. Mclaren F1 is not an entity to purchase anything. The Formula 1 teams uses Honda engines, but what I think you were meaning, THE Mclaren F1, the legendary supercar has a BMW V12.
пиздатые... интересно почему мерседес, порше, ауди, бмв и тд не делают модели авто с 1000 и более сил и всем остальным ультраспорт... ведь с их технологической базой можно эту топорную сборку переплюнуть на много порядков....
Salute to Mr Von Koenigsegg.
I prefer Koenigsegg Agera than Bugatti Veyron,Lamborghini Aventador, Ferrari's.