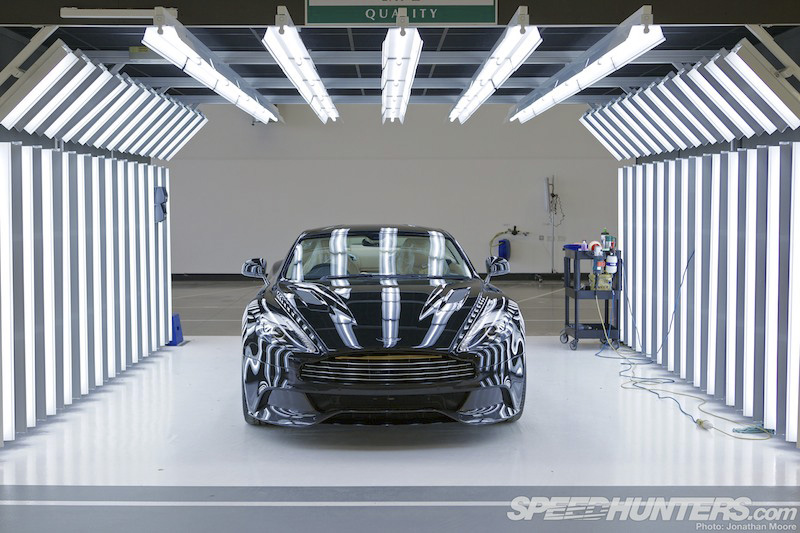
The world is filled with evocative car brands, but few with so rich a history – both on and off the track – and such a record for elegant design as Aston Martin. 2013 sees the company mark its 100 year anniversary and as part of its centenary celebrations, we’re dedicating the next couple of days to the esteemed English marque. And so, to kick off the theme, we wanted to give you an exclusive factory tour of the Aston Martin production line at Gaydon in the UK.
Factory doesn’t actually seem the right word for it though. That implies mass-produced items. Stamped out, identical products made to a set specification, repeated endlessly, dehumanised. That’s certainly no way to talk about an Aston Martin, always something that sets a standard for beauty and quality in an increasingly homogenised world. There are machines at Gaydon, there is noise and lots of people – and they do make things. But every Aston Martin is individually handcrafted, and here’s where they do it. If it is a factory, it’s a dream factory.
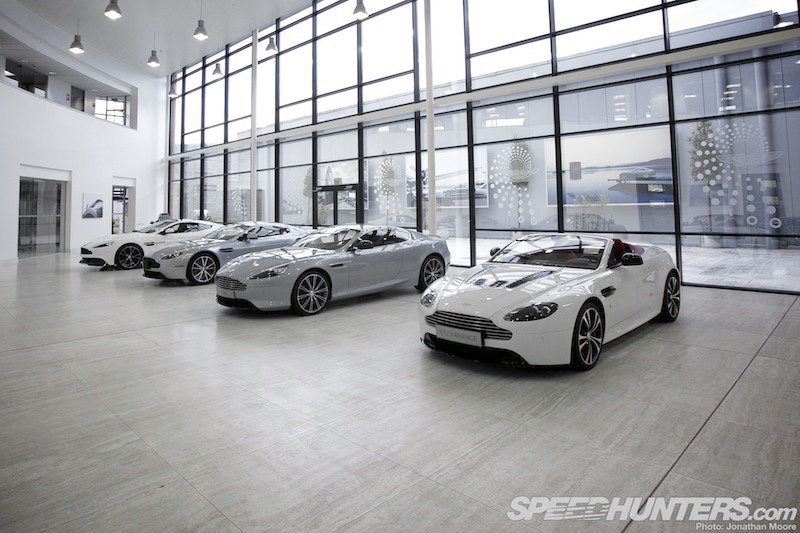
Aston Martin build and sell almost 4,000 cars a year, which means about 15-20 cars roll out of Gaydon every day. Although that’s not insubstantial, the bespoke nature of Aston Martin is reinforced when you compare that against a company like Porsche, who sell almost twice as many cars every year than Aston Martin have in a century. That just helps add to the mystique around Aston: barely 1,000 were built of even iconic models like the DB5. It’s just not about numbers.
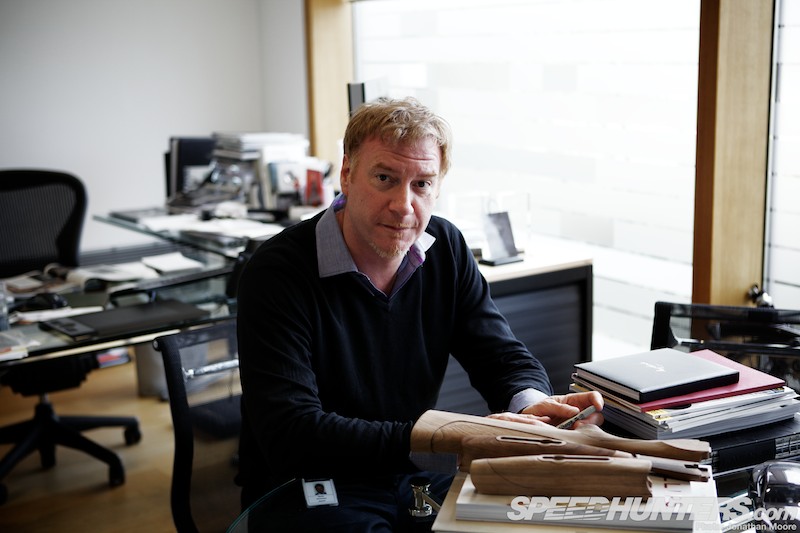
The man with the responsibility of not only guarding the brand’s heritage but taking it forward is Director Of Design Marek Reichman. He works with his team of 50 designers, stylists, craftsmen and engineers in a spacious studio right by the manufacturing plant. With a dozen models in the Aston Martin range, the new, seemingly unlimited ‘you ask, we make’ Q options range and then one-off specials like the CC100, the design department is always flat out.
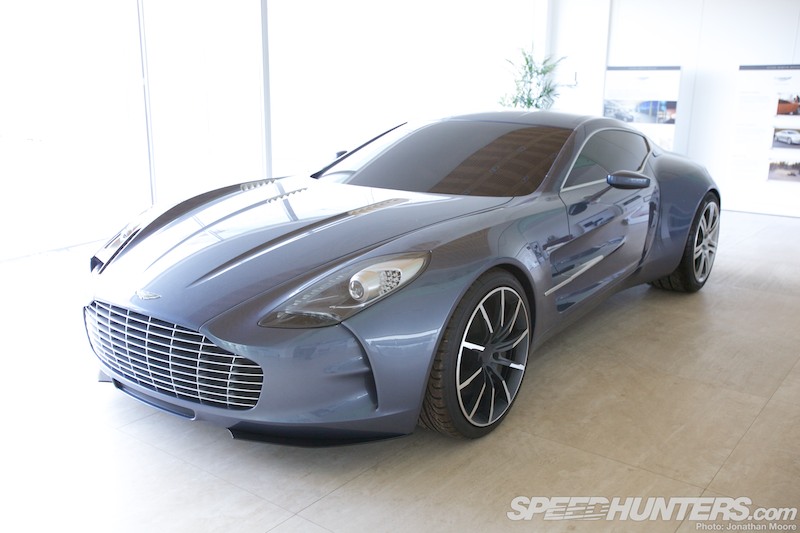
In the foyer of the design studio is this One-77 – and no ordinary One-77: this is the original full-size clay model, which takes some getting used to once you know. Clay?! It looks like you can open the door and drive off…
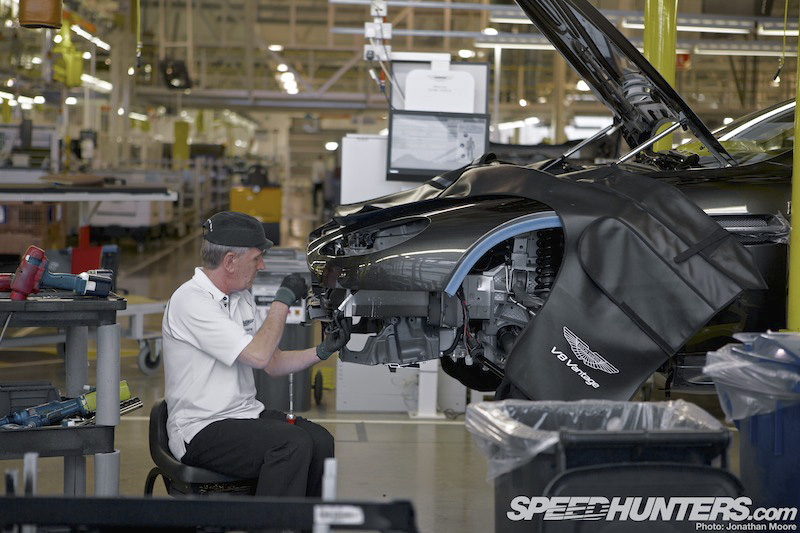
That’s been the ethos for all Aston Martins: to get it right on the inside, first you have to get it right on the outside. But once all that design work is done, it’s down to the skilled craftsmen on the factory floor to take the individual components and, like a massive and complex puzzle with infinite variations, put together the perfect sports car.
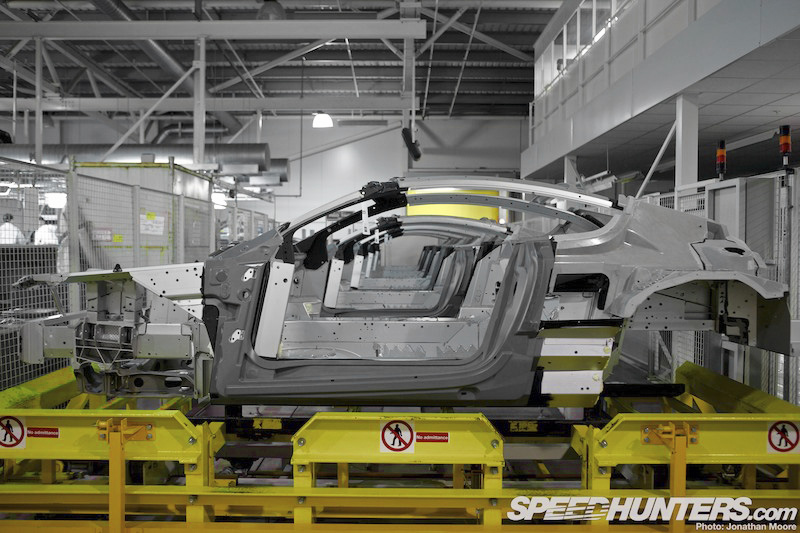
Aston Martin continue to use bonded and riveted aluminium monocoque at the core of their current range, utilising what they call the VH engineering philosophy. Vertical/Horizontal gives them a common platform which is easily scalable, using common systems and components where possible. The monocoques are constructed by a sub-contractor and shipped to Gaydon for assembly.
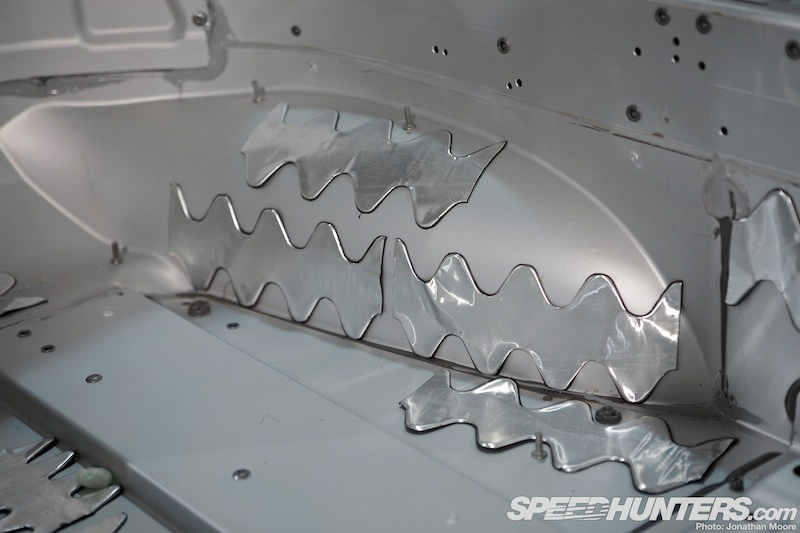
On these Vantage chassis I was interested to see these reinforcing strips added to the interior, applied as a result of noise, vibration and harshness studies to improve the characteristics of the chassis.
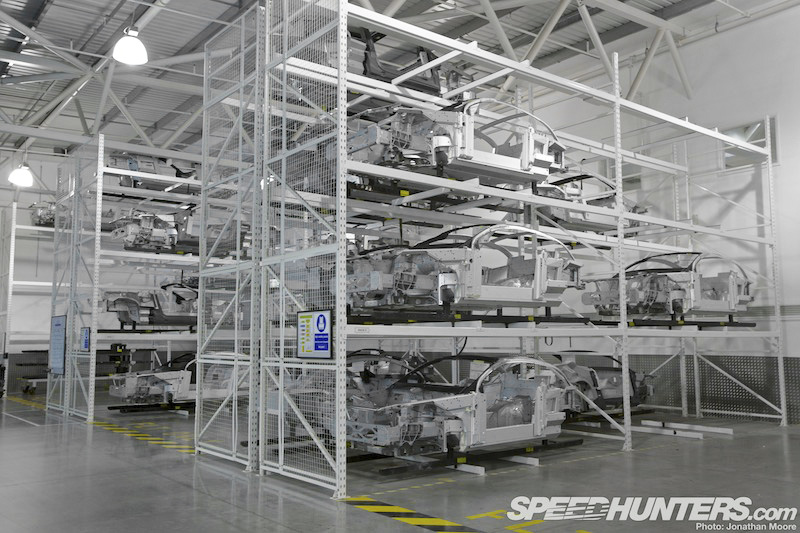
Once prepared, the chassis are stored on racks ready to be slotted into the production line: all cars are built to order.
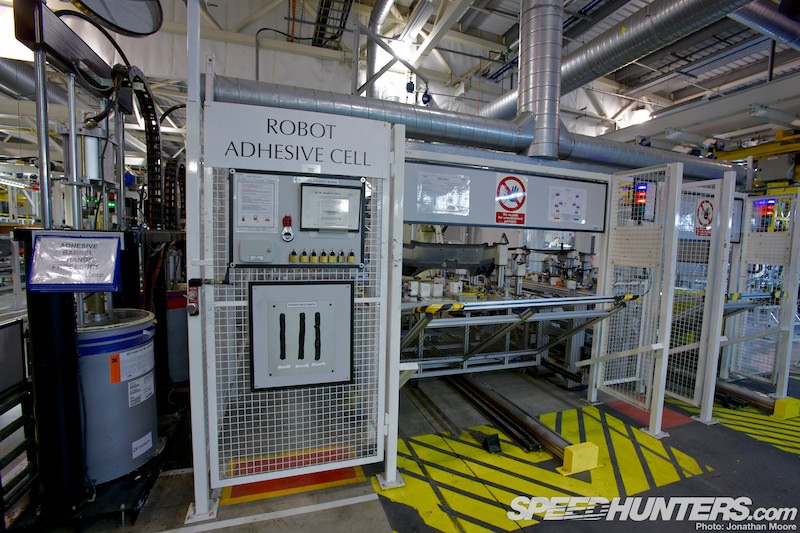
There are very few automated process across the lines, with just a few robots deployed. This machine applies bonding adhesive to the chassis, before the panels are manually slotted into place using a jig, heated and left to cure. Its name? James Bonder!
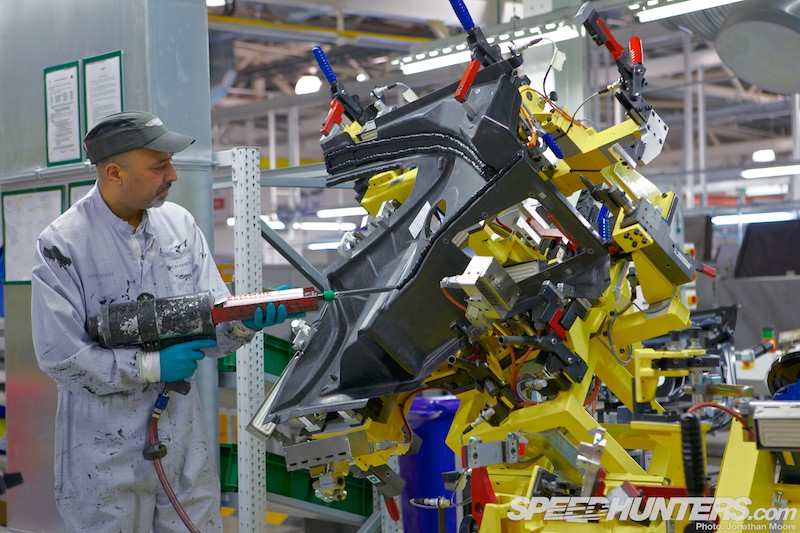
With so many special editions and new models, cars outside the core range have their own separate lines where specialist preparation is required, such as for the preparation and fitment of the carbon panels on the Vanquish.
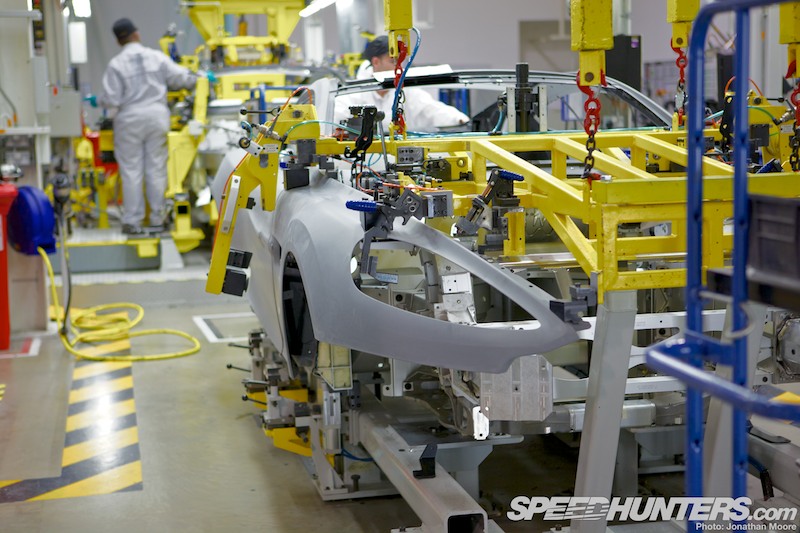
Allowed tolerances are minuscule, so a combination of visual checks and the jigs ensure an accurate starting point. The carbon panels require longer to bond cleanly, which is the reason why they’re attached on this separate line.
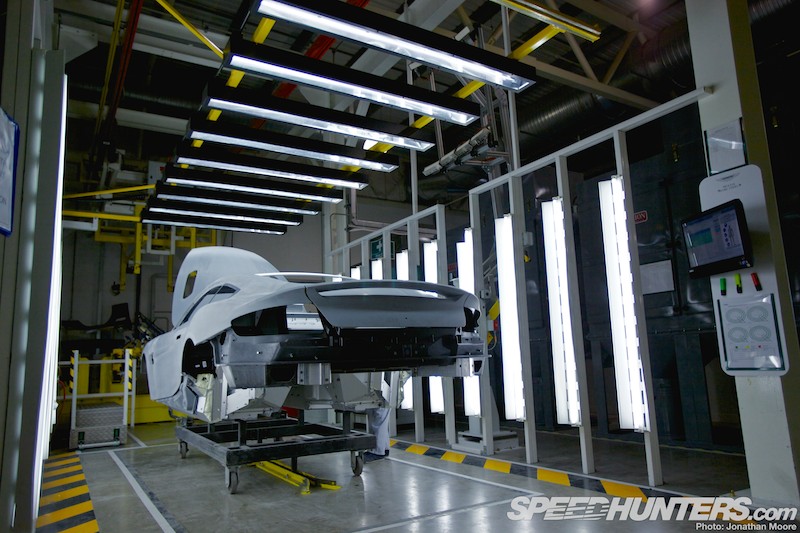
Every Body In White is thoroughly examined for surface defects before being shipped to the painting bays…
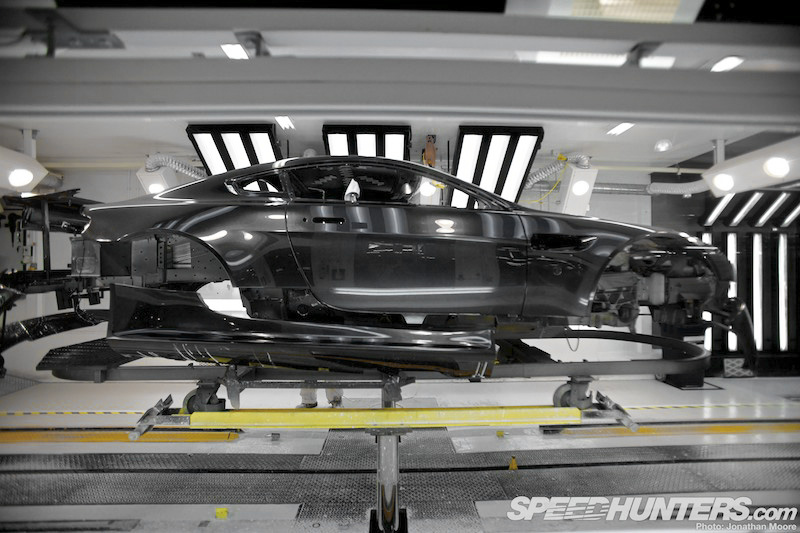
… where each car and its associated panels are painted at the same time to assure consistency. The paint process is long and laborious – which is the only way to get such beautiful and perfect finishes.
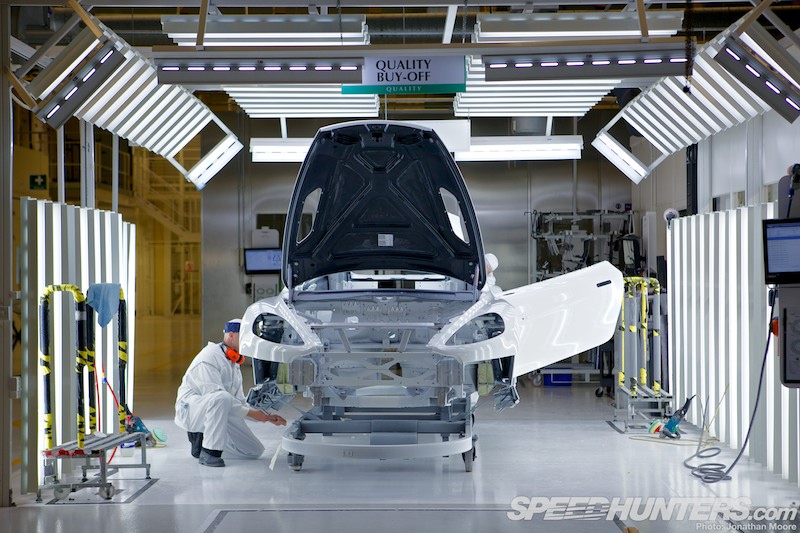
A Vanquish requires 50-60 hours in the paint shop alone, for example, and even a ‘normal’ paint job takes 25 hours to complete! Quality is repeatedly checked before sign-off for assembly can begin…
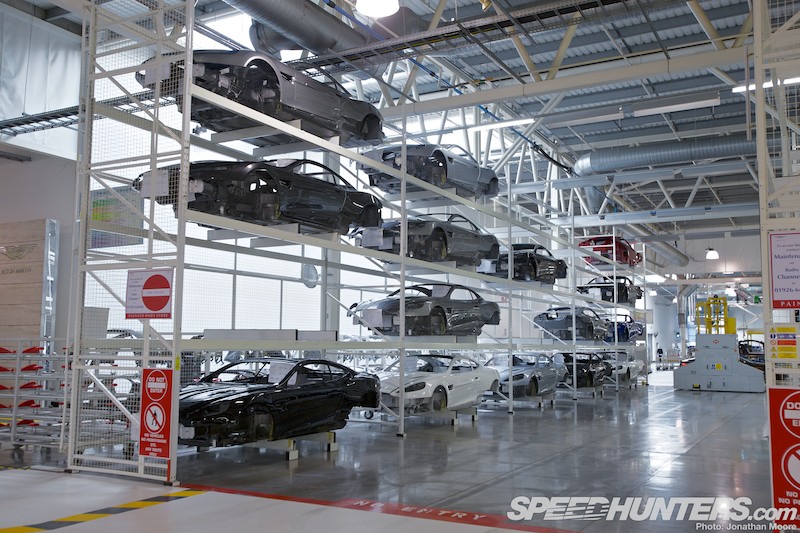
… and the painted shells loaded into another racking system…
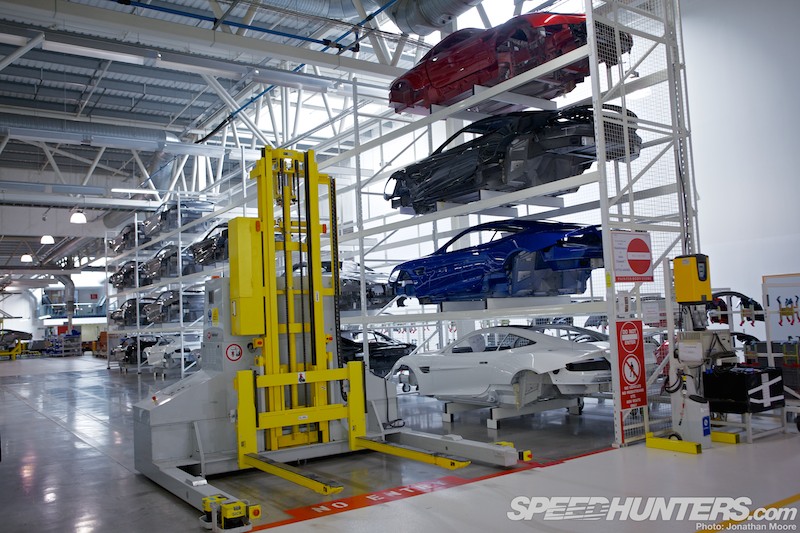
… which an auto-loader services 24-7. There are two main assembly lines, effectively split between V12 and V8 engined models, meeting at the middle for inspection and testing bays. I followed the V12 line round, which handled DB9s, Vantage V12s, Rapides and Zagatos.
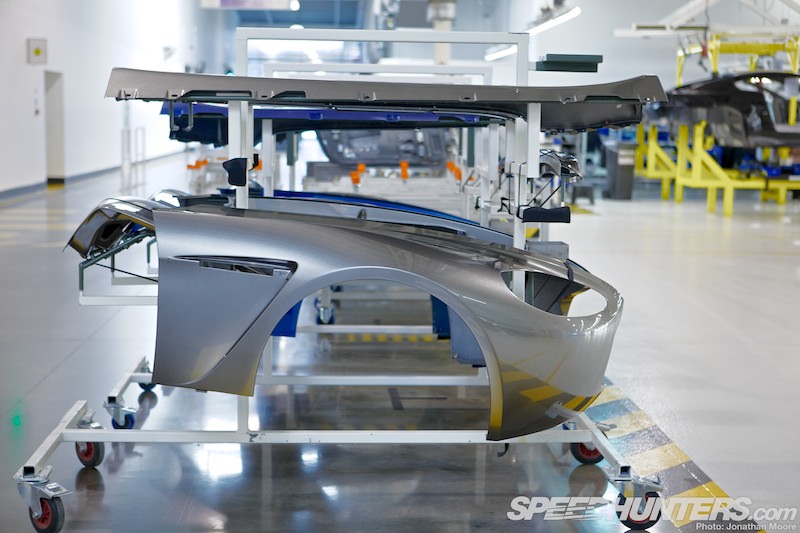
As the shells are called off, the doors, sills and bumpers are removed again to allow easier access.
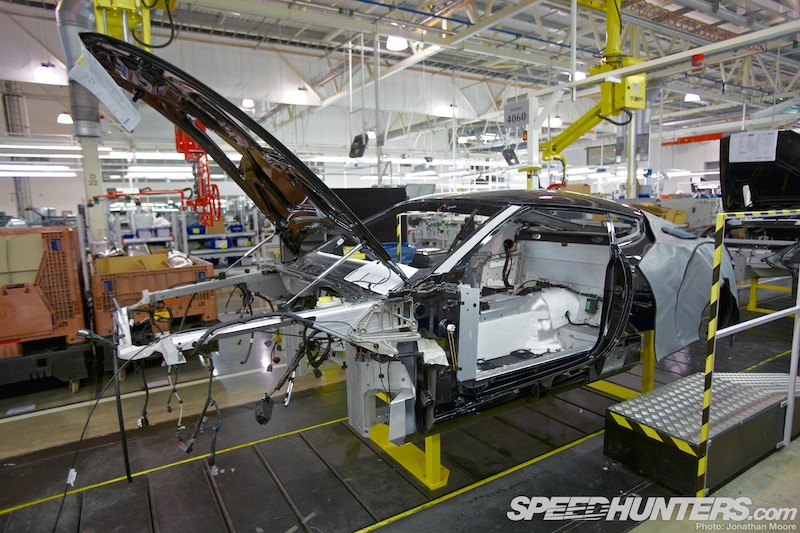
As is typical, the cars passed through stations along the line to be built up: staff typically train up on three stations and rotate every so often to make sure the skill levels remain high across the board.
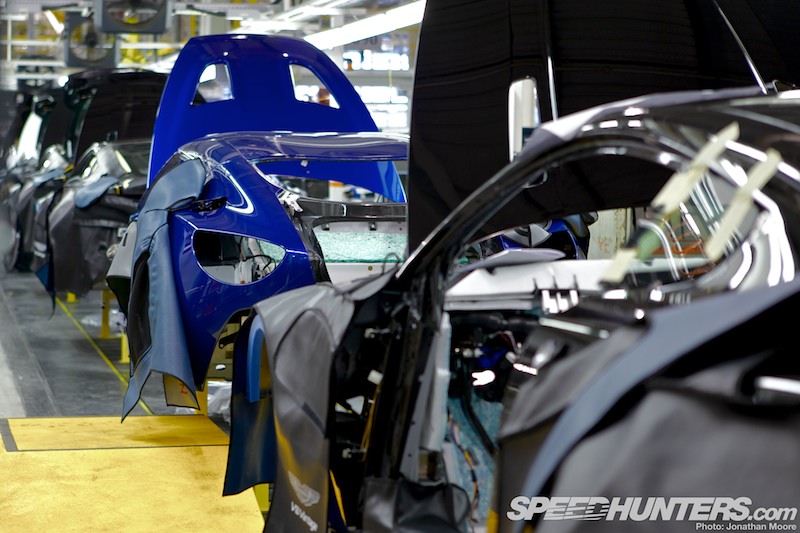
The One-77 had its own separate build unit (for all the 2,000 man-hours it required), and the majority of the base Zagato is now assembled there before. They’re slotted into the regular V12 production line for electrical and mechanical installations before being taken back to their own building for completion. The Zagatos were easy to spot in amongst the more staid colours of the other cars on the line that day…
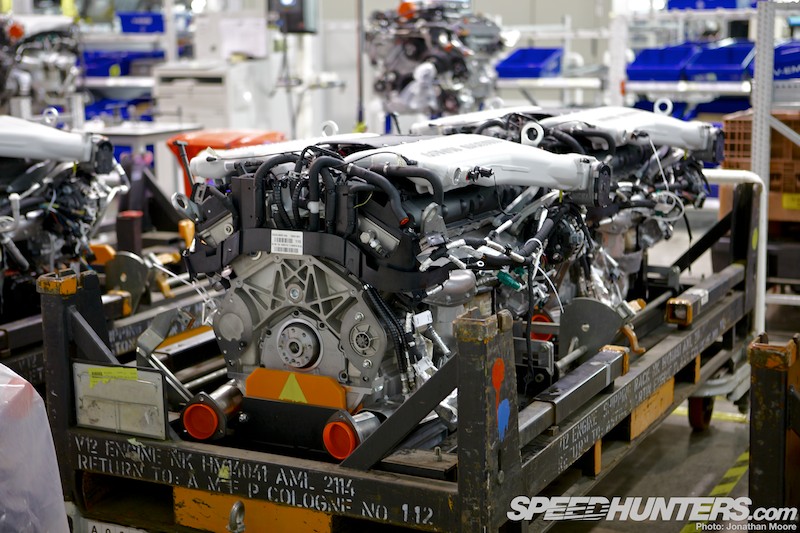
Parallel with the V12 assembly line is the engine and running gear area. The V8 and V12 units currently come in from Aston Martin’s production unit in Cologne, Germany – part of the Ford campus there – though a new deal has recently been struck with AMG to supply units in the future.
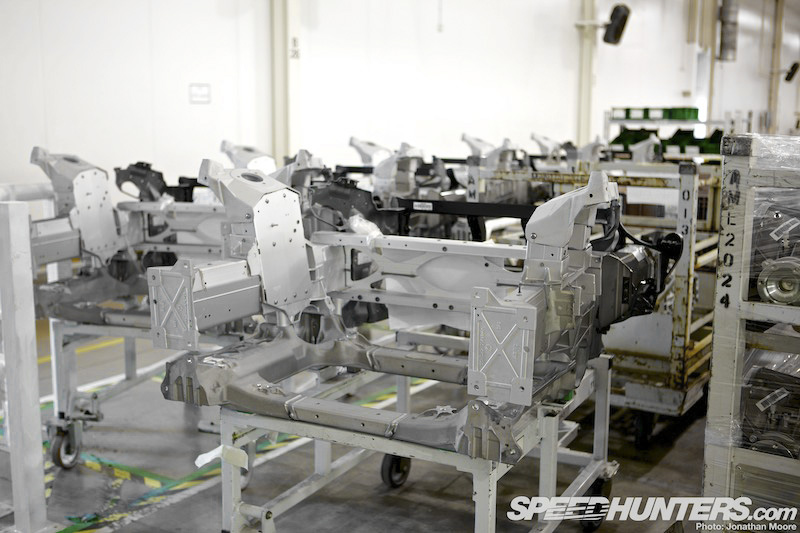
Sub assemblies and crash structures also come in pre-assembled.
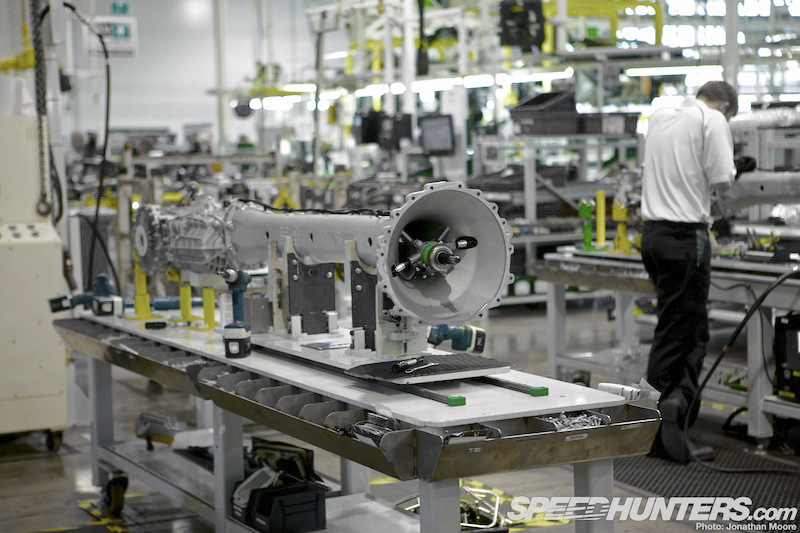
The team mate propshafts to gearboxes and engines to cooling and exhausts, and put together the front and rear suspension and brake systems.
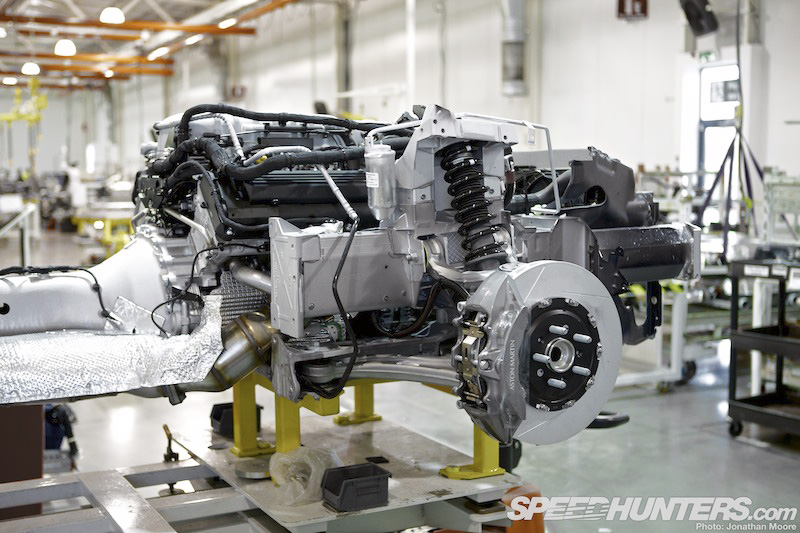
With the engines mounted in the front subframe, the suspension and control arms attached and the two ends connected with the torque tube…
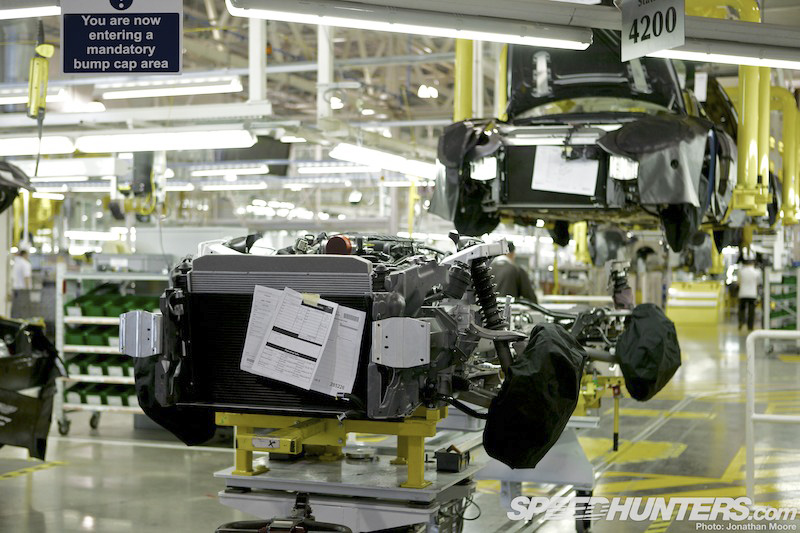
… the entire running gear substructure is then readied to be matched up with its matching shell.
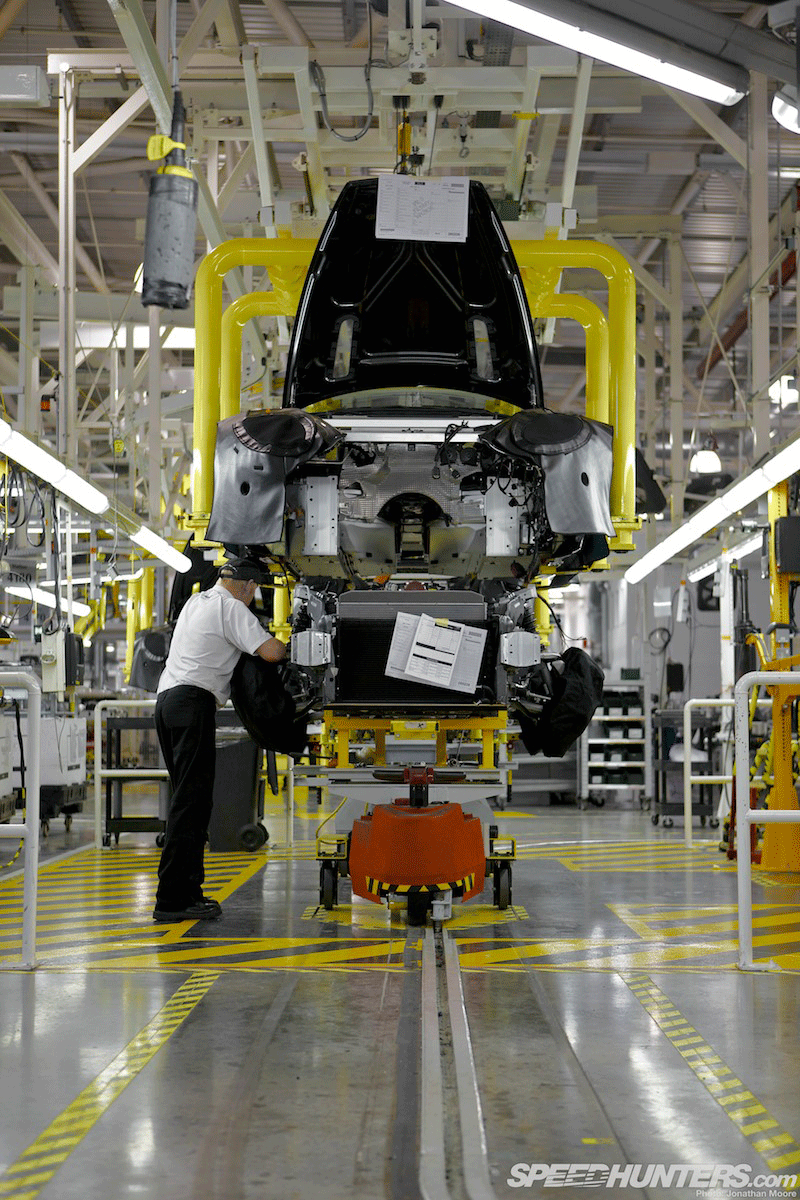
The team on that station then quickly bring the two together and the car can then be prepared for the return run down the opposite fixtures and finishing line.
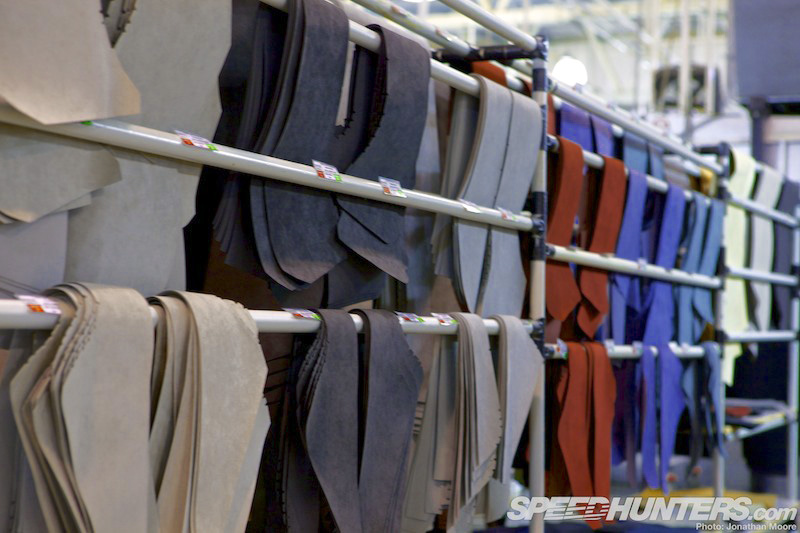
Meanwhile, the interiors have been given just as much care and attention. When I drove a Vanquish earlier this year I was stunned by the bespoke cockpit: it was truly a beautiful place to be. A large area at Gaydon is dedicated to the cabin trim, with stitchers working from kits of material (always cut from a single hide) to create each interior. A single person is responsible for one car’s cabin, to retain consistency and keep a connection with the car they’re working on.
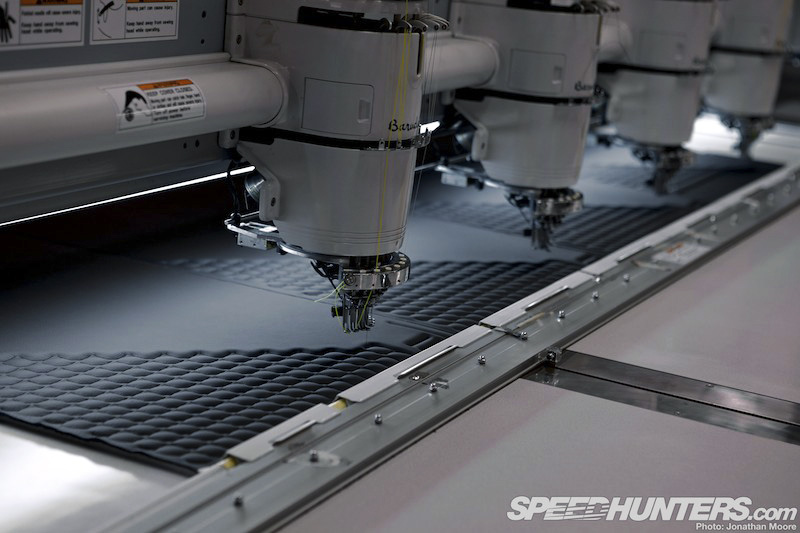
Quilting used to be done by hand, but now a row of machines has sped up that process – which when you think that some of the interiors contain over a million stitches is no bad thing!
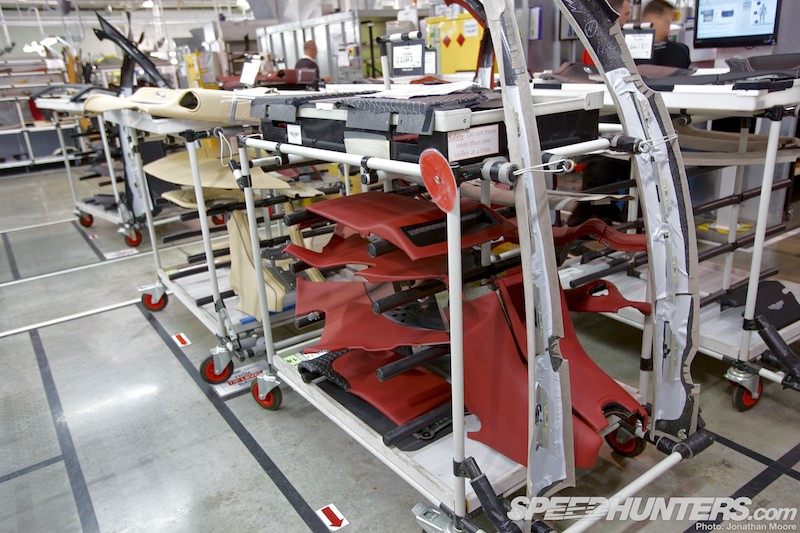
As with the panels earlier in the process, the finished interior trims are coded and put together on a trolley ready to be wheeled round to the waiting car and installed.
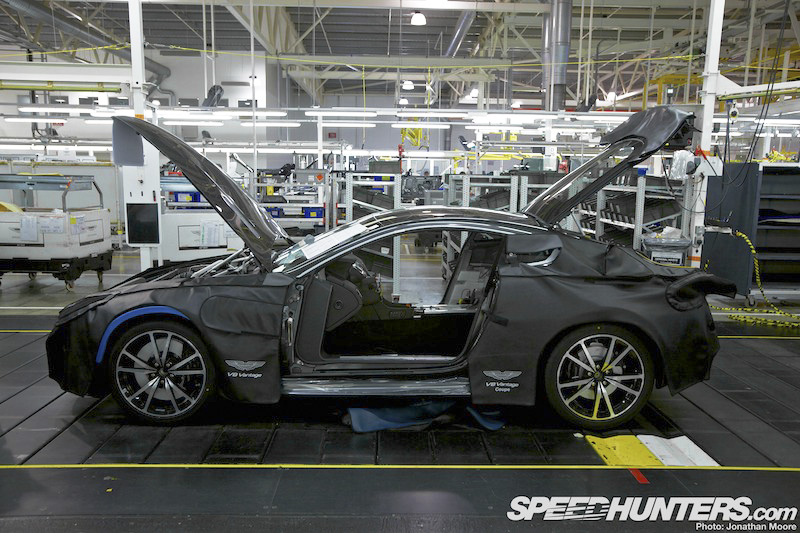
With the wheels on, the car can finally support itself and be rolled along, but there’s still the full cabin to be installed and wired.
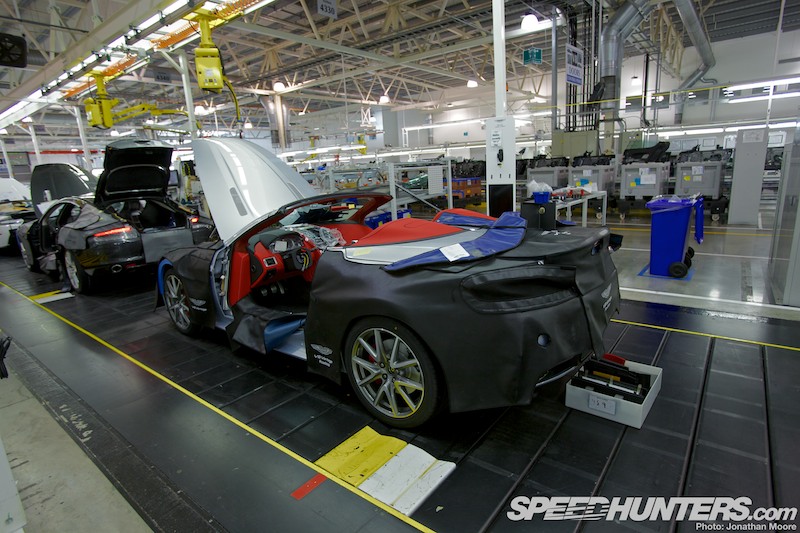
The different variants of cars follow each other through in a seemingly random order: convertible follows Rapide follows DB9… It seemed like there were never the same two cars together, which must make working on the line anything but monotonous.
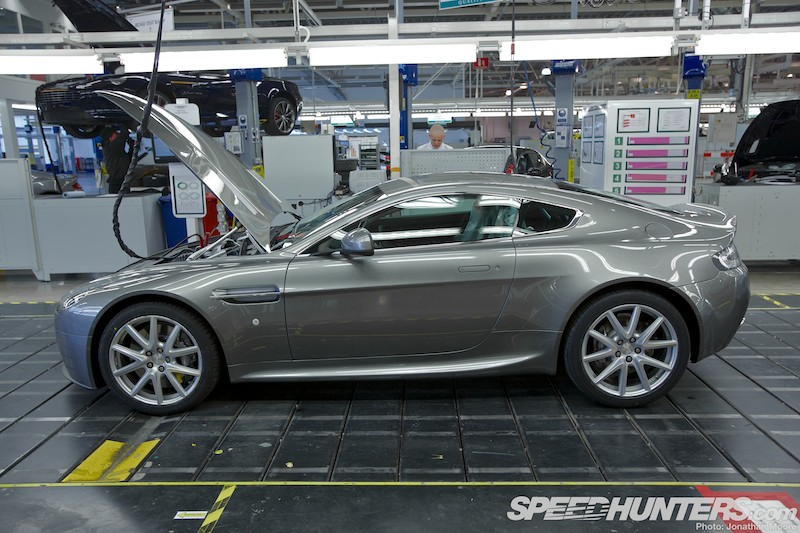
The doors are assembled separately and then attached, and final electrics installed before the external umbilical can be detached and the heart of the new baby Aston allowed to beat on its own.
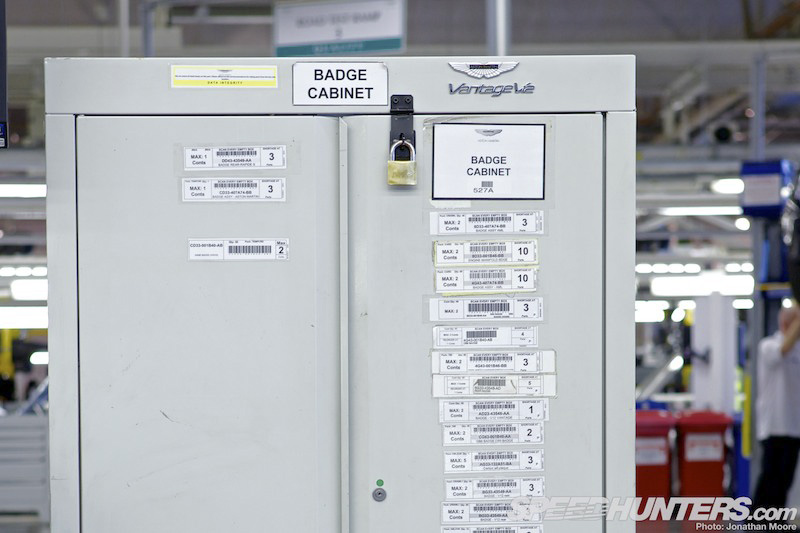
Like a badge of honour the iconic Aston Martin wings aren’t attached until the very end.
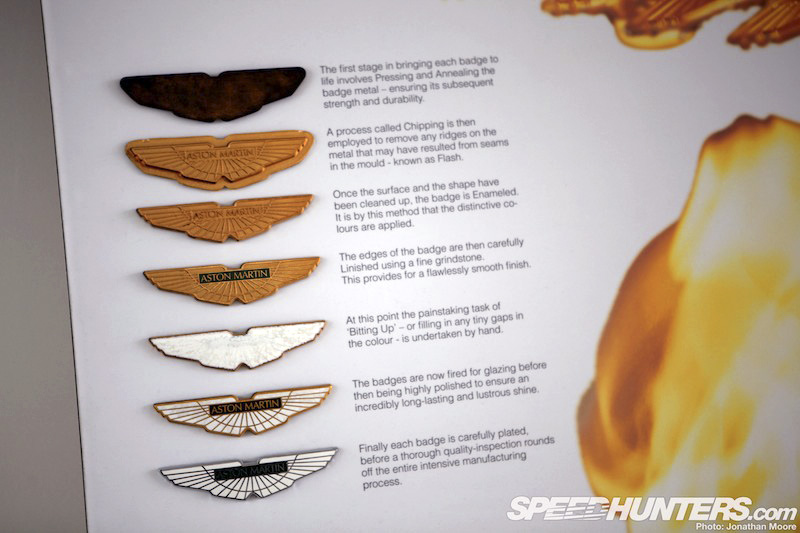
All the badges are now created by a single specialist firm in the jewellery quarter in nearby Birmingham: each one is hand-finished and then, of course, applied by hand to the nose of the car.
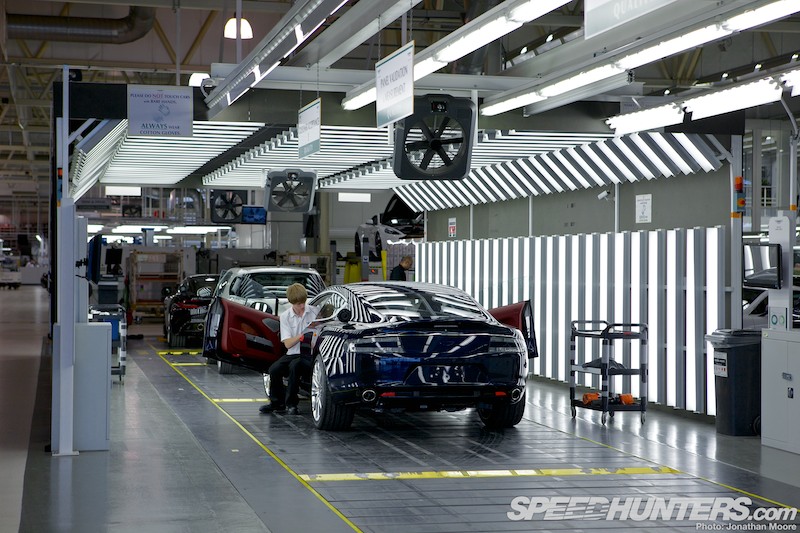
But although the hard work of manual assembly might be over, testing has only just begun. Each car is put through a vigorous set of inspections and tests, with visual checks of the exterior…
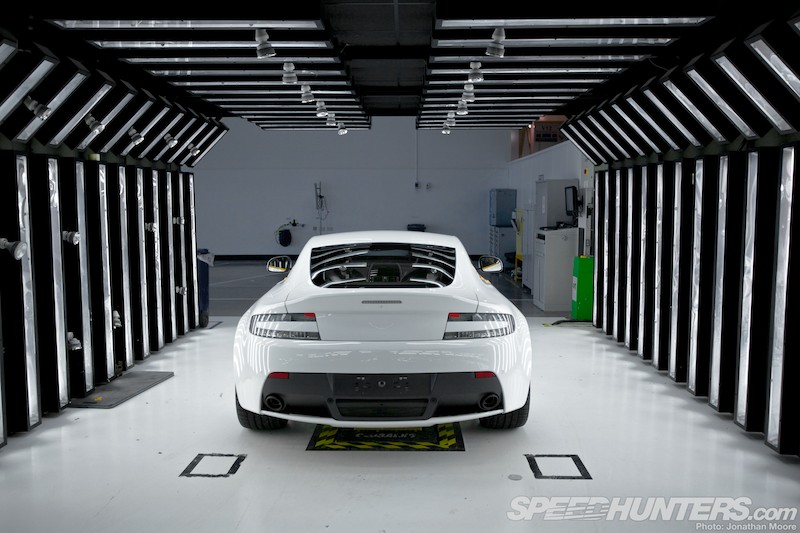
… along with rigorous electrical and mechanical checks before the car is run out on the adjoining Jaguar/Land Rover test track.
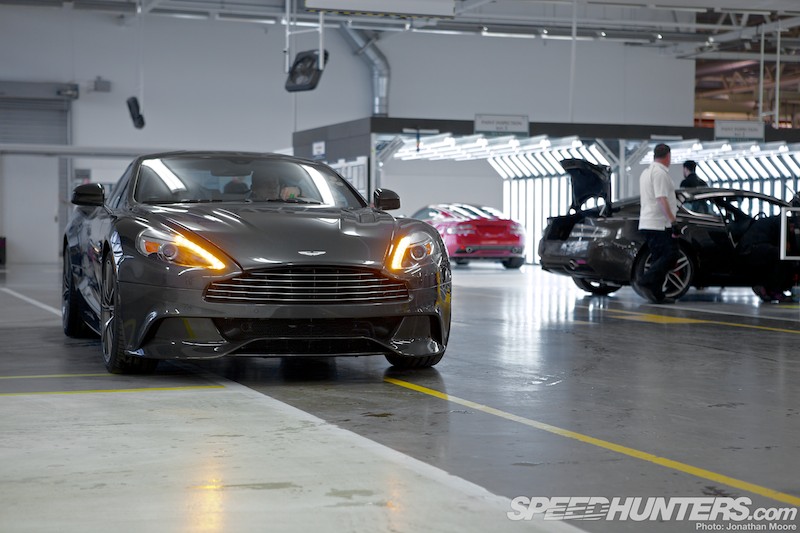
Finally, 200 hours later, you have an Aston Martin. I think it would be worth the wait…
Although you won’t have to wait long for more coverage from us! Make sure you stick around over the next couple of days for our Aston Martin theme here on Speedhunters – there’s plenty more to come.
Jonathan Moore
Instagram: speedhunters_jonathan
jonathan@speedhunters.com
Aston Martin theme on Speedhunters
More Aston Martin stories on Speedhunters
The DBS is retired and that sucks. The flagship of them all. The worst thing they ever did was retire that car. It was the best one they ever made.
I own and love a DB9 Volante. On my next visit to the U.K., I would very much enjoy a factory tour. Is such possible?