
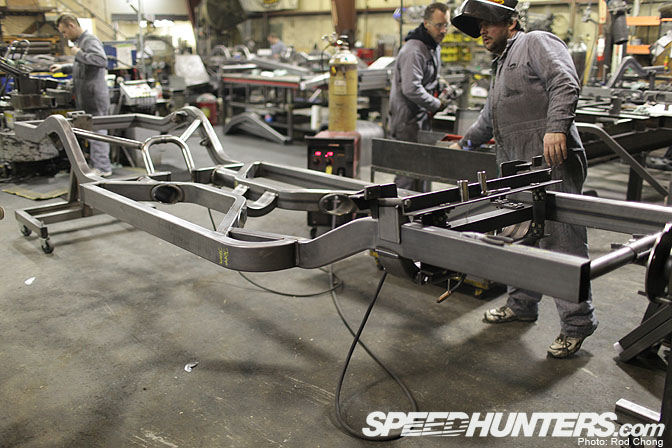
Those of you who are following the progress on the Team NFS Mustang RTR-X build may be interested to learn a bit more about the company that did up the custom front sub-frame for us: Art Morrison Enterprises.
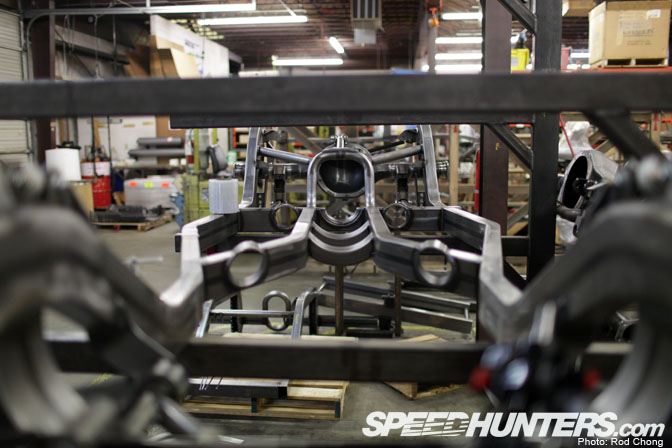
Any readers of Hot Rod magazine will of course recognize the Art Morrison name as being top dog in the aftermarket chassis industry for muscle cars and classics.
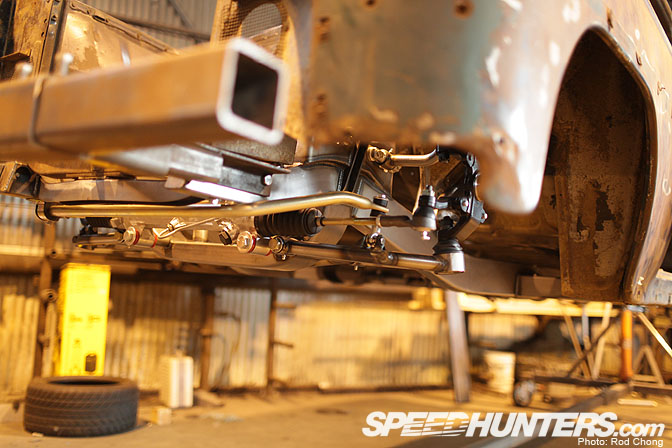
Some of their aftermarket chassis are designed to bolt straight into popular body types like this 1954 Chevy. You then choose the suspension type and AME will do the rest.
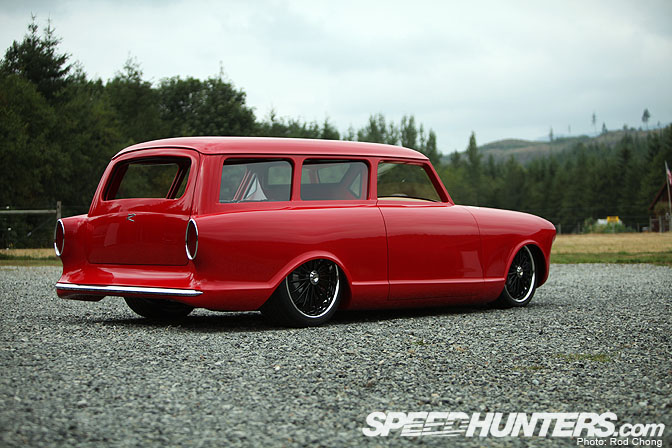
In other cases, like the the crazy Ferrambo build, a bespoke chassis may be needed and Art Morrison Enterprises can create practically any configuration required.
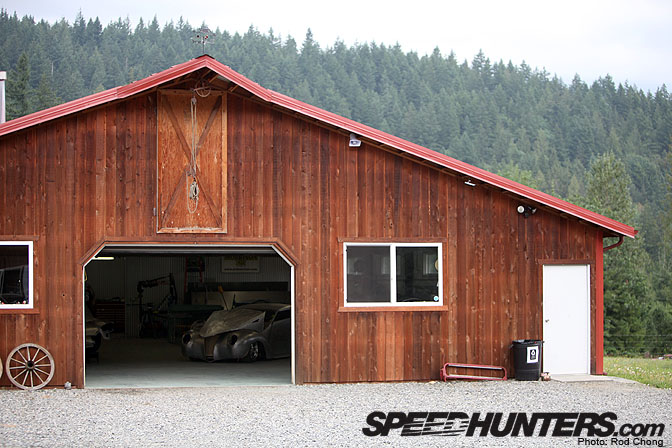
Interestingly, we first met Craig Morrison, Art’s son, while shooting at Divers Street Rods outside of Seattle, Washington. A rapport was instantly established and we were invited to come visit their Tacoma manufacturing facility.
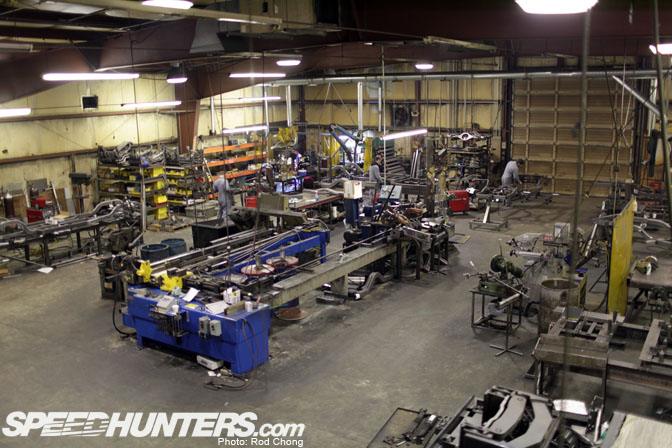
And this is the warehouse where it all happens. Art Morrison started out building tub frame drag cars, and this is the same location that was used to manufacture these chassis back in the ’70s and early ’80s.
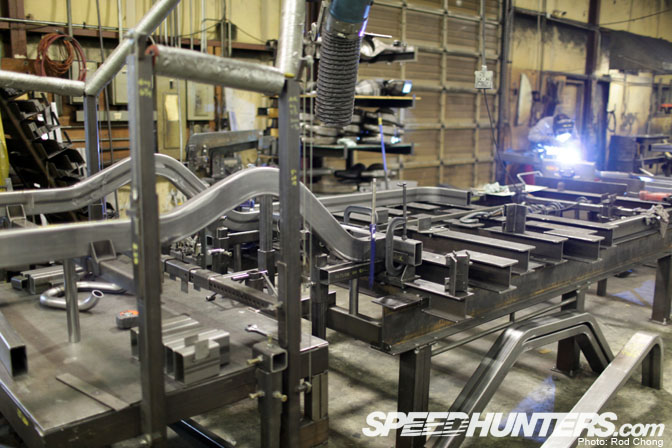
Here you can see the beginning stages of an AME chassis laid out on one of the many jig tables.
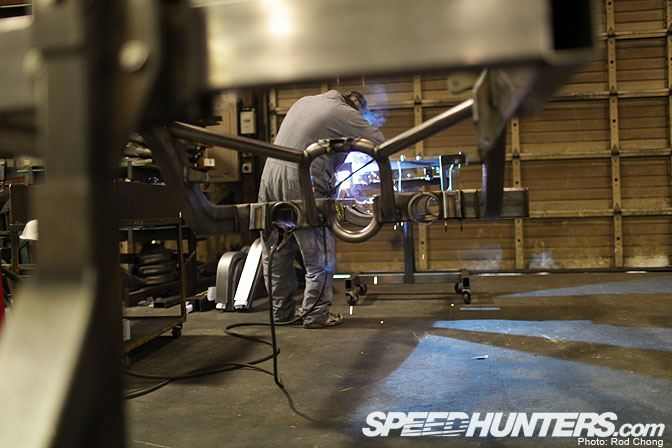
This view of the chassis shows the through-frame exhaust holes to aid in ground clearance. A lot of these chassis end up on Pro Touring or Kustom style cars, both of which require ultra-slammed stance. The chassis designs take this into account complete with the option of air bags and optimized suspension geometry for low slung driving.
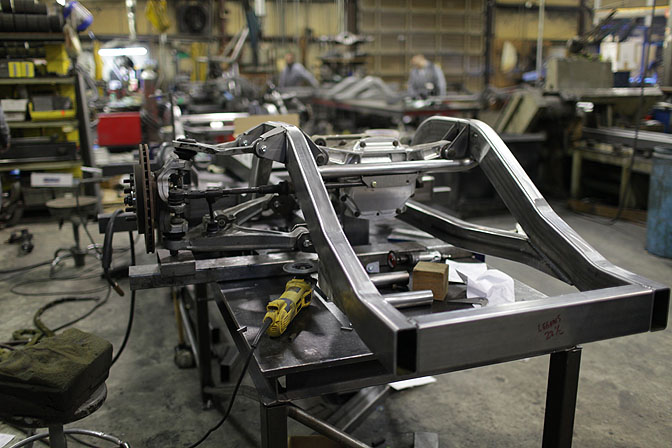
This shot shows the type of custom chassis fabrication that AME can do for their customers. This set up is having a late model Viper IRS installed for a 1950’s era Chrysler hot rod.
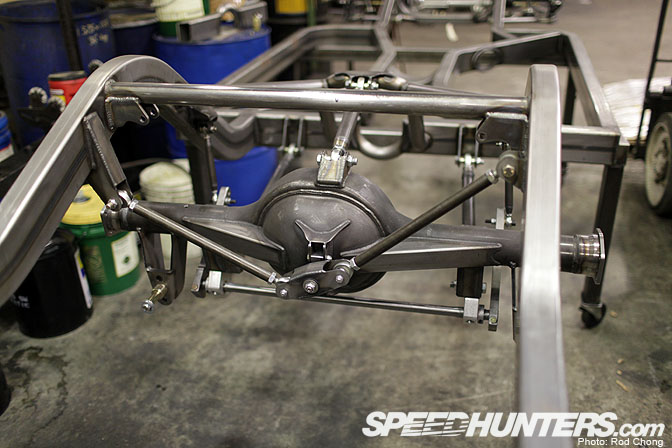
When selecting one’s suspension setup you can denote if the car should be optimized for the race track, drag racing or bags. This three link suspension allows a solid axle a wide range of articulation best suited to Pro Touring style builds and track day enthusiasts. The bell crank on the rear end housing is vertical when the suspension is at ride height.
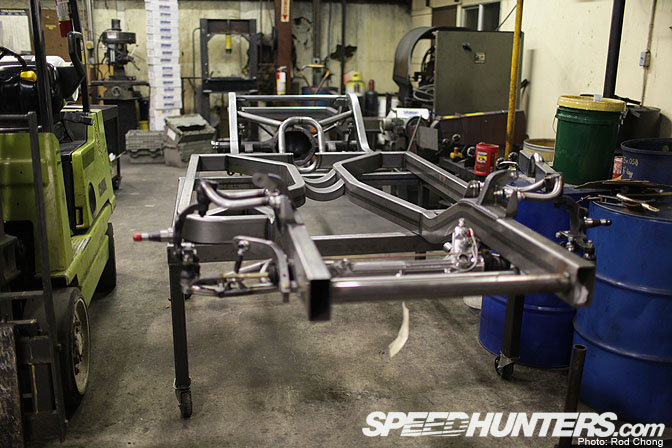
The front of this chassis features AME’s latest IFS and a splined anti-sway bar. The car is a 1964 Ford Falcon that will be widened 2” and stretched 4”.
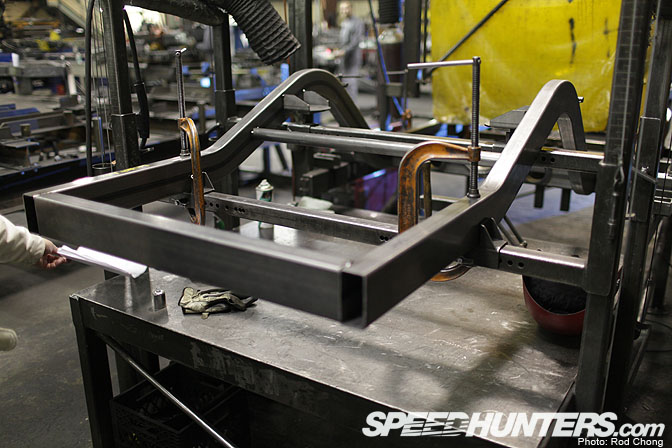
This assembly is destined to be attached to a ’67 Barracuda.
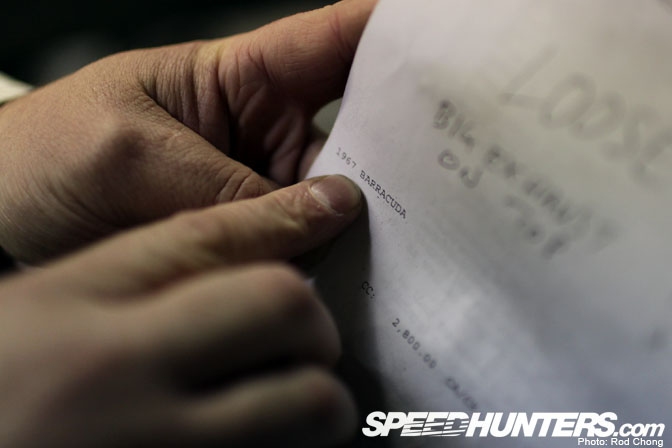
We took a moment to look at the customer paperwork for the project.
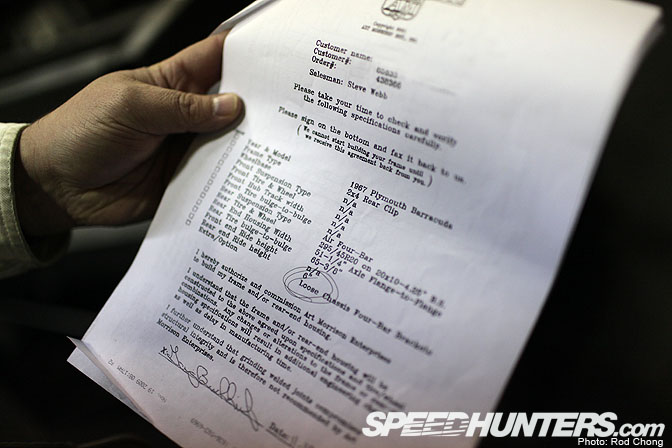
As part of the build sheet is a check off list specifying all the critical components of the customer’s order.
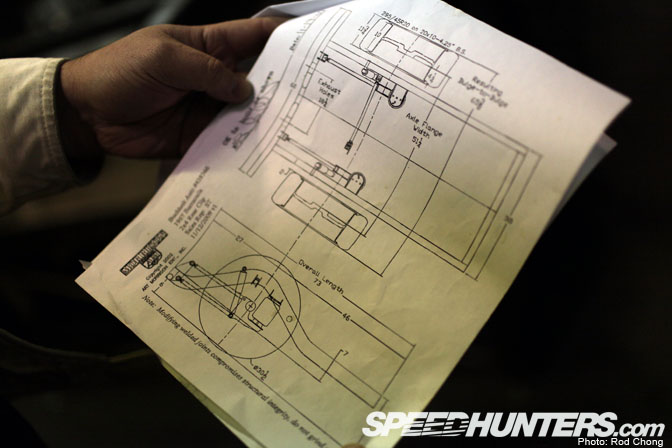
The CAD designed chassis information also accompanies the order showing all critical dimensions that were specificed by the customer. This shows the suspension details too…
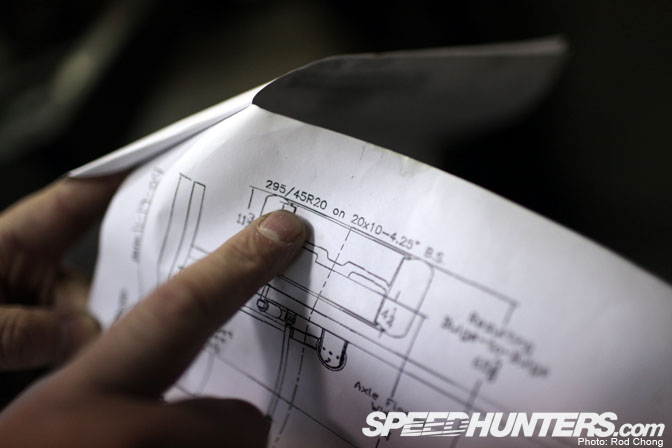
… as well as tire and wheel sizing, to ensure proper tire/wheel fitment and geometry.
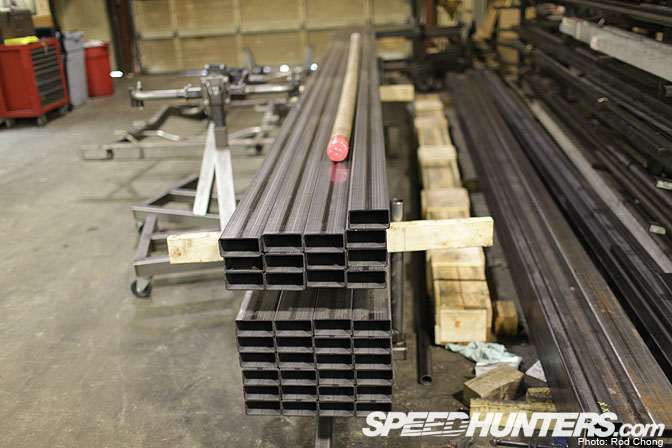
The foundation of Art Morrison Enterprises Inc. chassis is 2”x4” rectangular tubing. It is custom rolled for the company and comes in 20’ length.
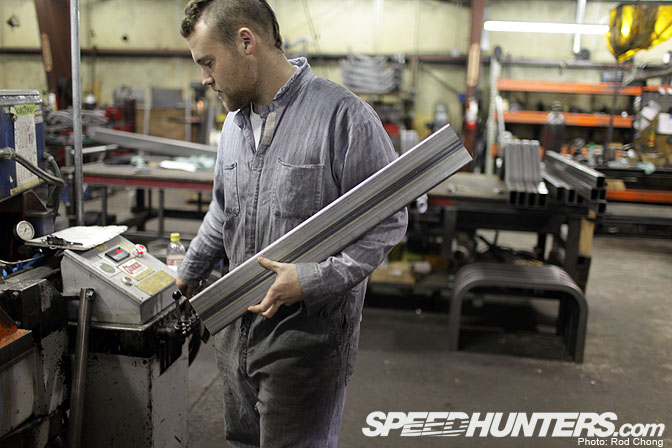
Mandrel bending technology is the key to the construction of AME’s frame design. Here a length of 2”x4” tubing is getting ready to be loaded onto one of the two in-house benders.
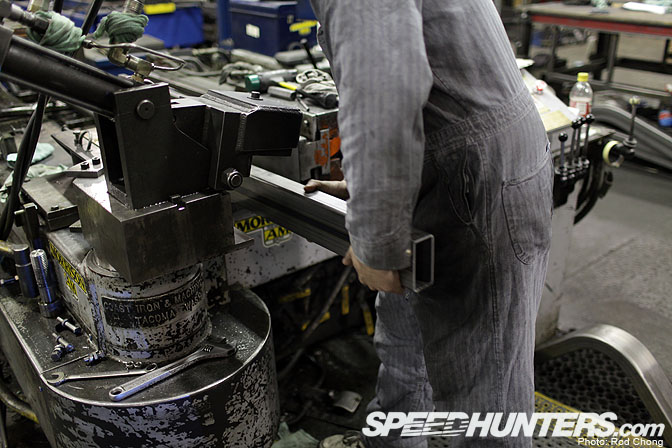
Sliding the tube over the mandrel die ensures that the tube will be supported on the inside of the tube and eliminates any chance of the tube wrinkling.
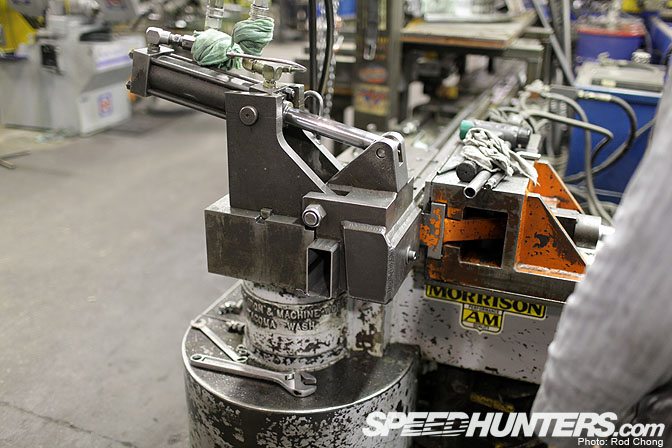
The clamp then holds the tubing against the bend-die supporting the tubing on the outside. Supported on both the inside and outside the tube is drawn around the bend die.
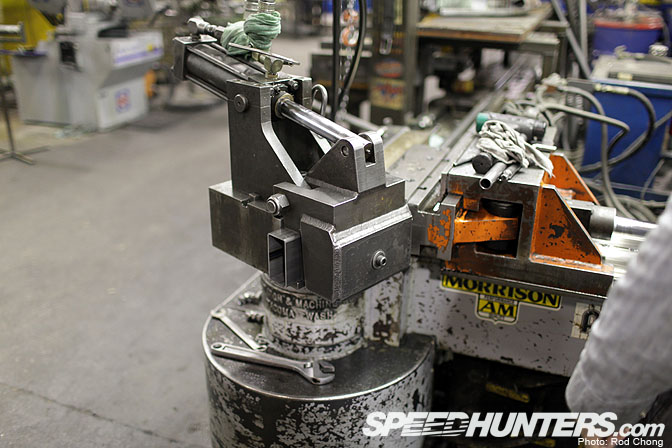
As the tube is bent it rotates around the bend die while the wiper die supports the back edge of the tubing.
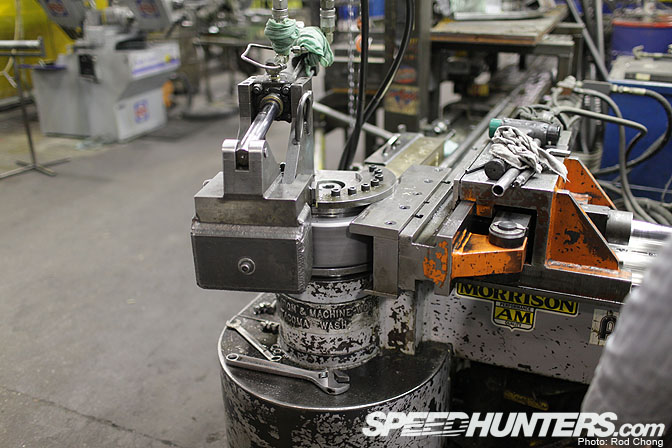
The clamp die also follows the tubing out to help eliminate any possibility of the tube wrinkling.
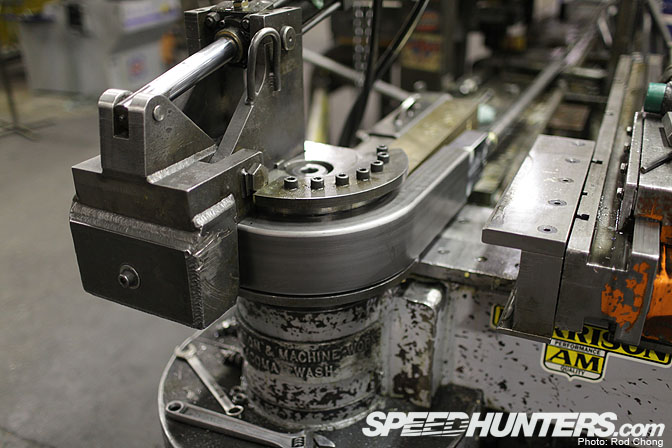
Now that the bend is done the clamp die is removed showing the wrinkle-free bend.

Now bent, this center “X” support will be trimmed and installed in a chassis.
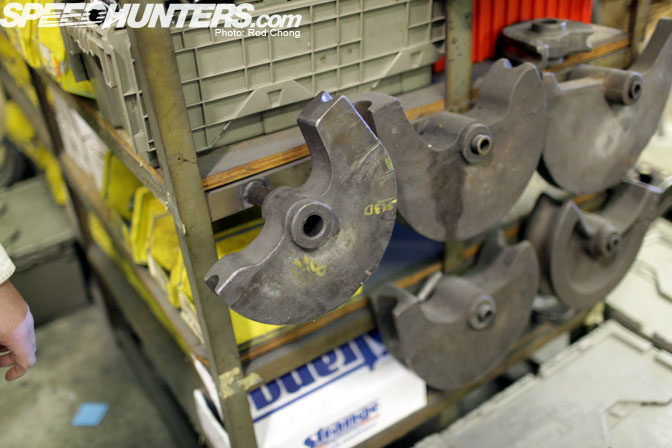
In addition to 2”x”4” tubing, AME also bends up a number of different diameter round tubing sizes for roll bars and roll cages as well as their SuperCar line of all round-tube drag race chassis.
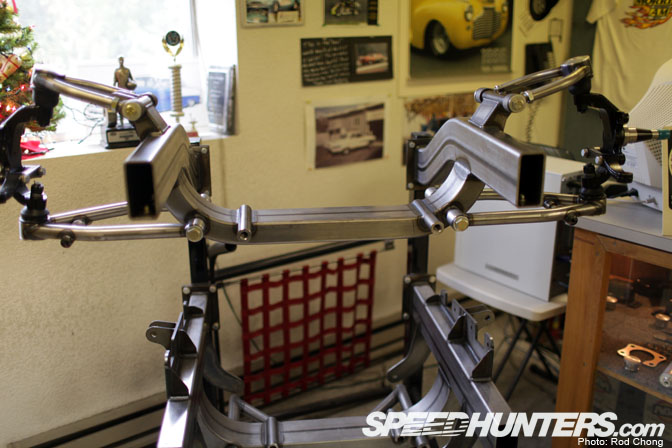
We also nosed around their offices… this is one of their display items showcasing some front clip/suspension setups.
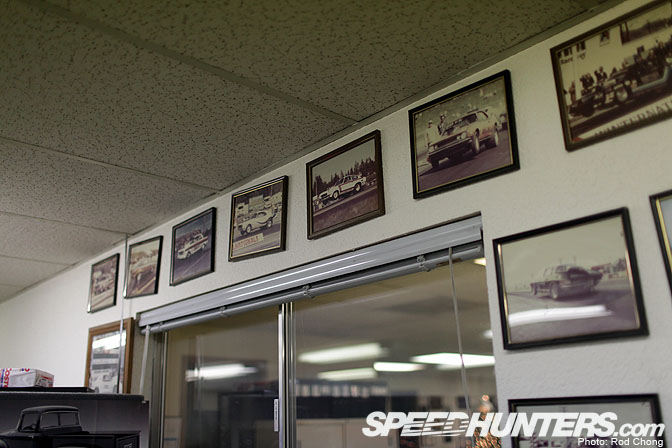
In the showroom is a collection of pictures of some of the race cars built by Art Morrison Enterprises Inc. back in the day.
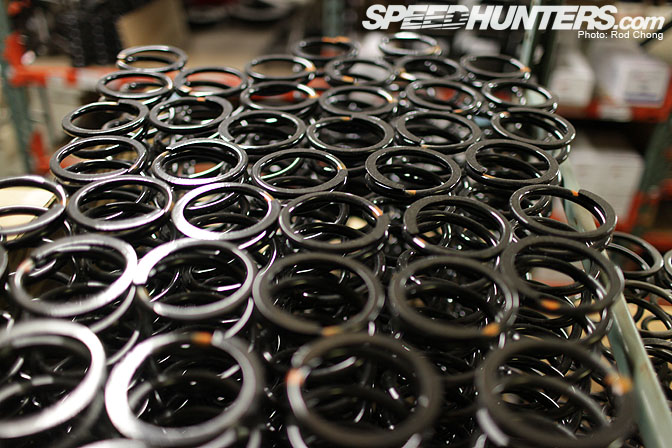
It was also fun to check out the parts warehouse…
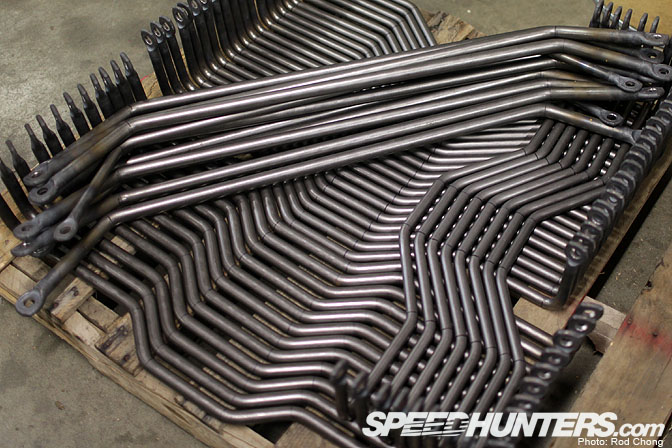
Here’s a pallet of newly formed anti-sway bars ready to go out for plating.
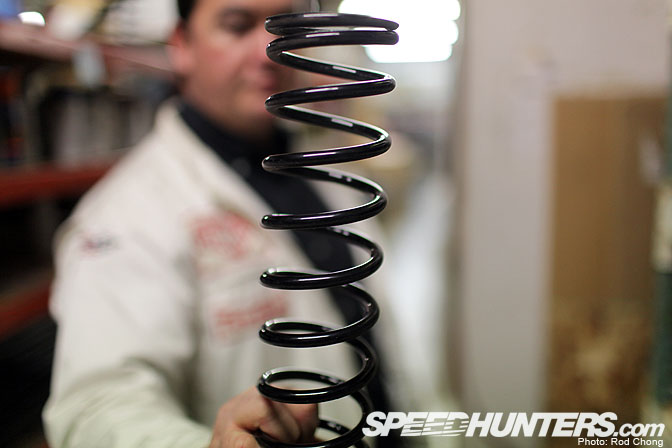
In addition to heavy coil springs for road course duty, AME also stocks light weight springs for drag racing. Here an 80# coil is shown.
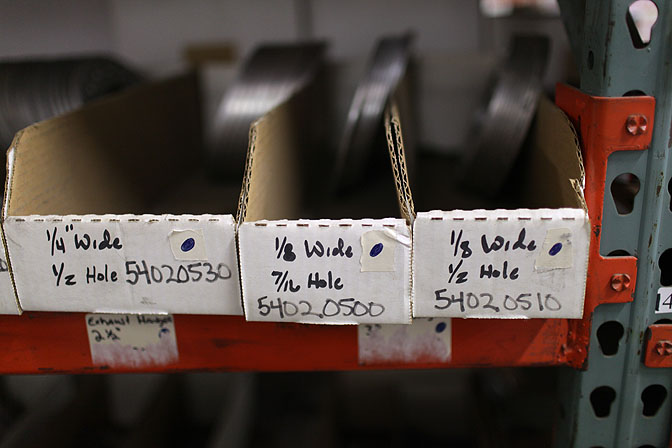
If adjustments are needed for wheel fitment, AME stocks a wide range of wheel spacers.
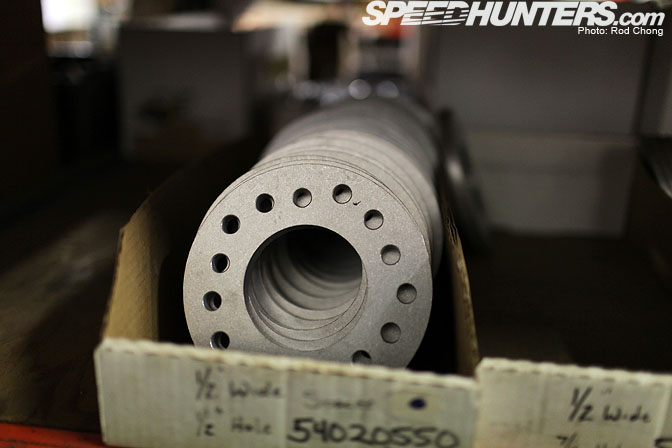
Drilled for the popular domestic bolt patterns, these wheel spacers are machined in house on AME’s cnc machinery.
Crated up for shipment, this early Corvette chassis awaits the freight truck.
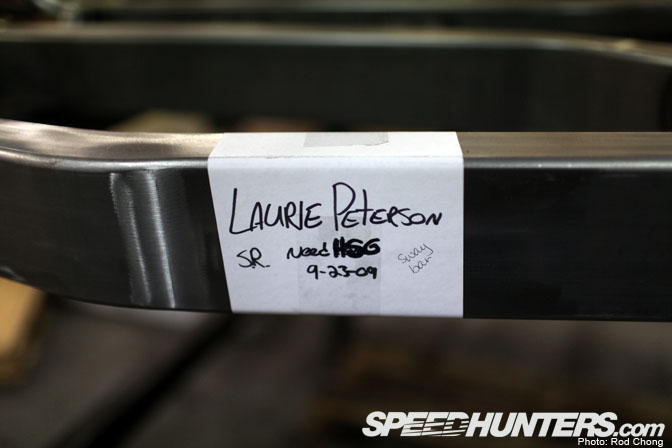
Canadian customer Laurie Peterson’s chassis sits on the rack awaiting the final pieces to be mated up to the chassis. The car is a 1962 Studebaker Avanti that will be powered by a very potent Chevrolet LS engine.
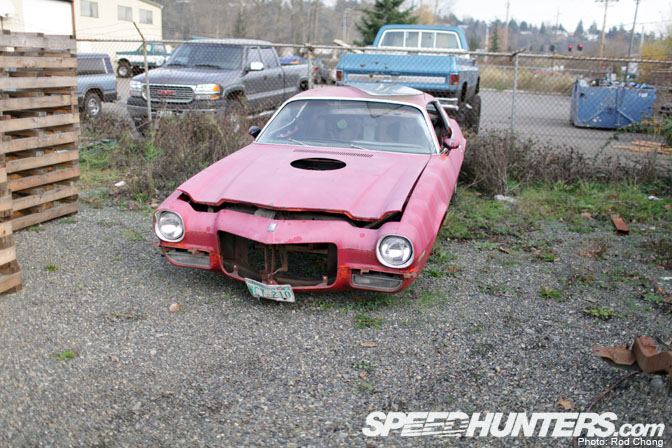
Out behind the AME warehouses are some interesting finds. This 2nd Gen Camaro (1970-1981) was used to design a replacement front subframe featuring C6 Corvette suspension components.
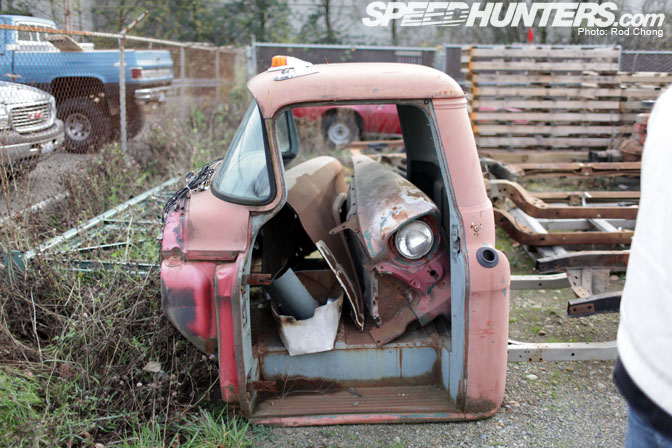
An early Chevrolet truck cab that was used to provide cab mount information.
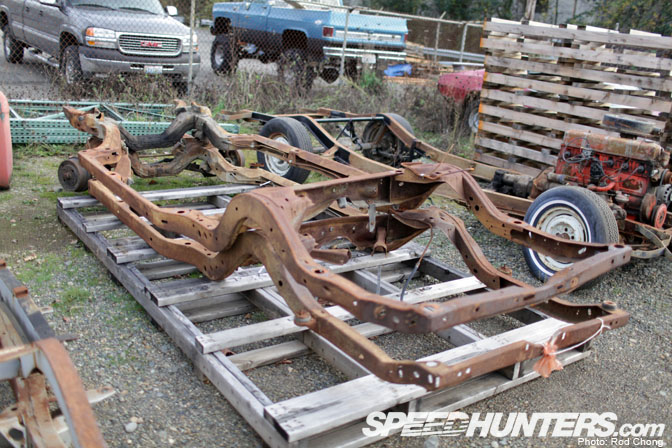
A double stack of 70’s era Chevelle chassis provide the reverse-engineering information needed to create a new high-performance replacement chassis. Note how flimsy these chassis look compared to the modern AME aftermarket items!
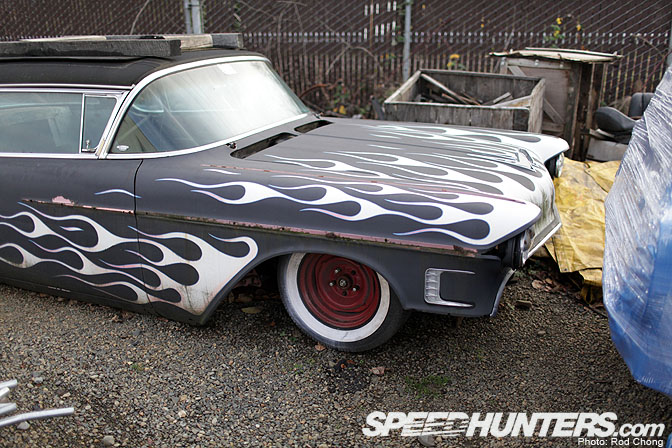
This wild 1958 Cadillac project belongs to one of the employees of Art Morrison Enterprises Inc. and features a custom air-spring chassis to achieve this level of ride height.
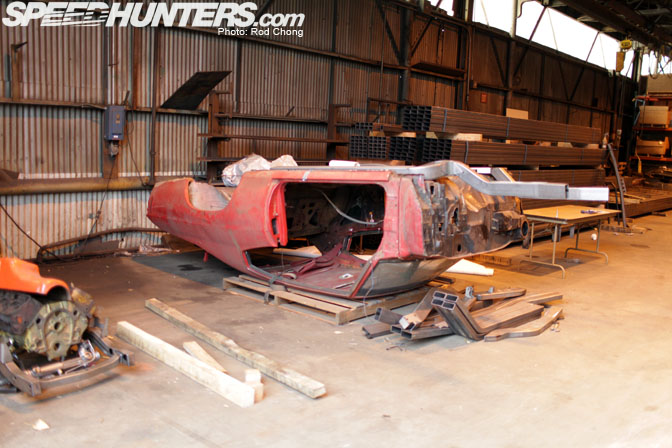
In addition to the chassis, a Chevelle body was sourced to hand fit the chassis to the body. Because the roof was already damaged it made for an easy platform to flip over and use as a work bench.
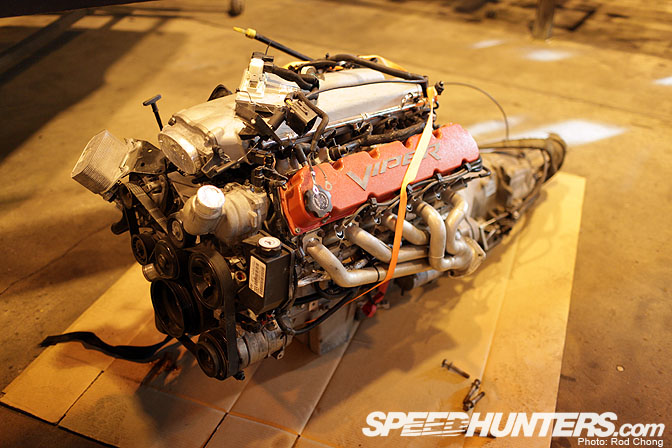
As part of a custom chassis for a very rare 1948 Chrysler Town & Country, this late model Viper engine will be part of the drivetrain package.
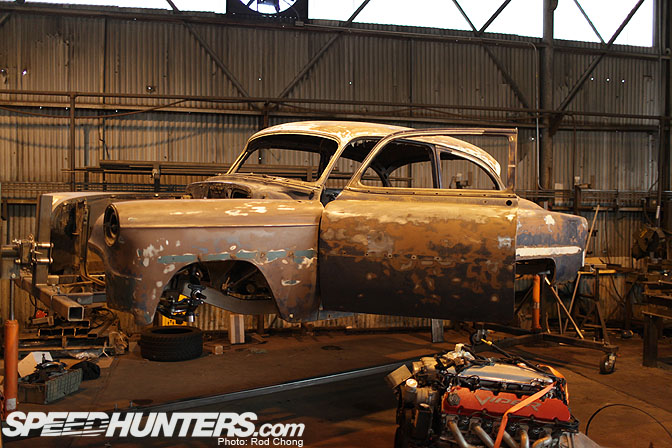
This is what most hot rodders start off with: a body style that they like and begin to modernize as their own tastes and wallets dictate.
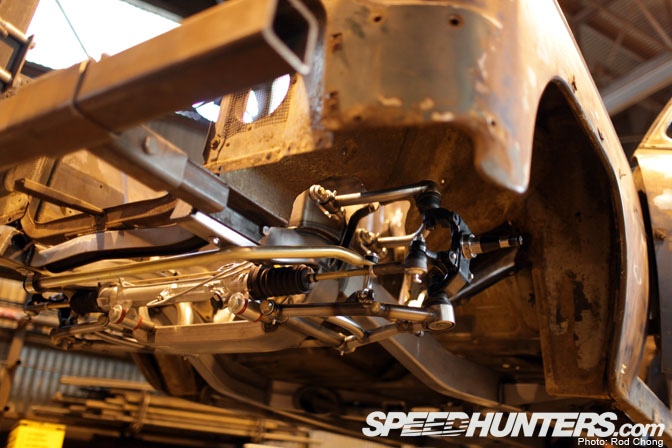
The long short arm front suspension and rack & pinion steering will breathe new life into the performance and handling of this old Chevy.
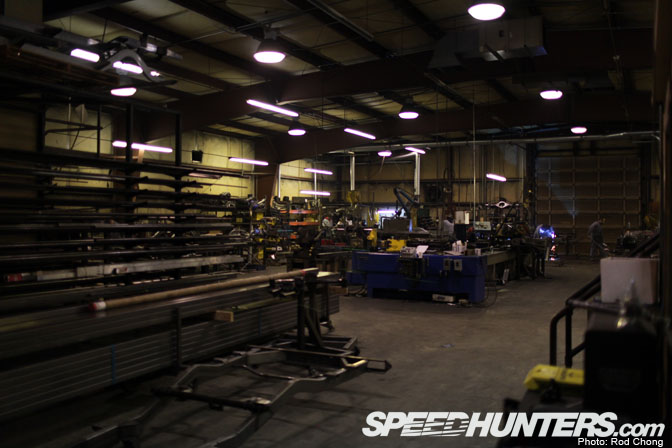
I’d like to thank Craig Morrison for taking the time to give us a tour of the AME facility and caption most of these photos! We also need to thank AME for getting involved with the RTR-X project. Cheers guys!
:R
Saw these guys on an old episode of American Hotrod last night! Amazing skills!
whaaaaaa
Wow.......amazing
AMMMMMMMMMMMMMMMMMMMMMMMMMMMMMMMMMMMMMMMMAAAAAAAAAAAAAAAAAAAAAAAZZZZZZZZZZZZZZZZZZZZZZZZZIIIIIIIIIIIIIIIIIIIIIINNNNNNNNNNNNNNNNNNNNNNNNNNGGGGGGGGGGGGGGGGGGGGGGGGGGGGGG.
they are the genius behind closed doors
great story, I learned new things and photos are beautiful
i cant tell if the cadillac is out of its glory days or if its just starting them! i really needed the info this thread delivered! im a wiser man hahaha
What an awesome facility. I would do just about anything for that setup.
Great story Rod, love the behind the scenes view.
KICKASS!!!!
Respect !
Outstanding feature Rod !
i love the red camaro boday and the flamed cadilak oh ya i wonder what the viper motor is going to be used for?
Great work! I love it!
Love those guys so much. they have helped me out on numerous occasions. tons of love and respect for evey single person in that shop. AME guys always deliver no matter what!
A personal dream of mine is to have a custom steel frame made for my '62 Nova. With modern design being able to basically perfect the handling of any classic, I would be crazy not to. I want to make a real street machine. http://www.maxworthyfabrication.com.au
Amazing website, love classic kings,
air-conditioningsydney.com.au
jrobinson50659@gmail.com